Lead Time Syndrome
The flexibility of a supply chain or an operation is based on the time to change (or flex) capacity and the total cost to change. Automotive assembly lines may have a flex time of up to six months to change the output of cars per day and with a substantial cost.
The aim of Operations Planning (also called production planning and control) is to meet the Sales & Operations Planning (S&OP) targets concerning: reliability of due dates; shortest lead times; high capacity utilization and low work in progress (WIP) levels, while maintaining the productivity targets of the organisation.
An unexpected event like COVID 19 can increase the order load on a facility and the options available to accommodate new customer orders are reduced. Planners may increase the lead time and/or split orders into transfer batches to get some of the orders through the facility. Increasing lead times has risks and splitting orders may require more downtime for equipment changeovers, so capacity is reduced.
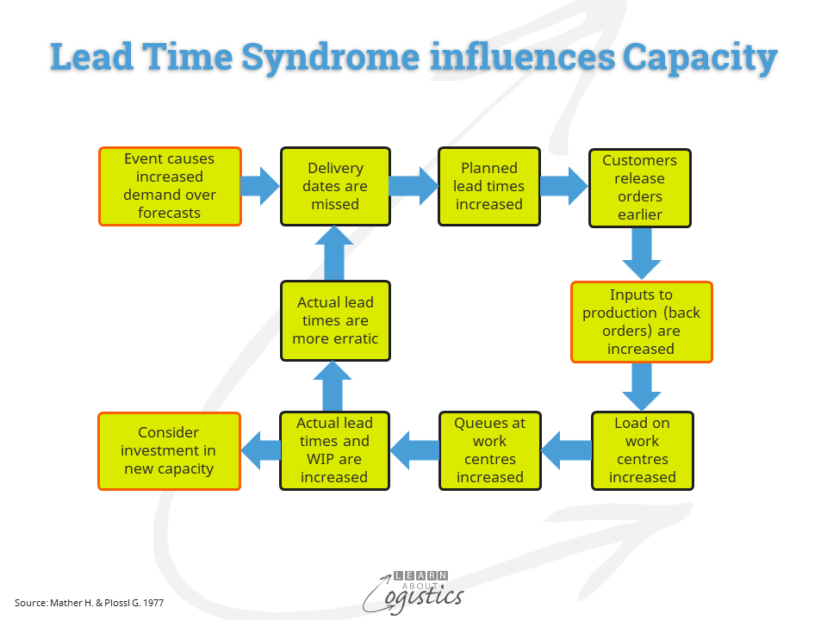
The effect of increasing lead times can cause a business to experience a cycle of missed delivery dates, as shown in the diagram. As delivery dates are missed and planners increase the planned lead times, customers are likely to order more items to cover the increased lead time. Back-orders will increase, as erratic ordering behaviour results in even larger variability.
A continual increase in lead times and back-orders makes this situation worse. Directors of the supplier business may even authorise construction of new facilities. Critically, when a new facility commences operations, capacity is increased and therefore the lead time for new orders is reduced. Consequently, as customers have already placed orders to cover the extended lead time, they have no need to place new orders. The supplier will progressively reduce the lead time to attract orders until the lead time falls to the original level. At worse, the new facility is then closed due the lack of orders – real demand has not substantially changed!
This outcome provides an example of the need for Supply Chain professionals to understand the interconnectedness of all elements through supply chains. In the situation of increased lead times, the interaction of variables, such as: capacities, planned and actual lead times, suppliers’ lead times, work in process levels etc., can lead to unforeseen problems when trying to meet the achievement targets.
The situation described is not hypothetical; it has occurred on more than one occasion, with severe consequences for the affected businesses and their people. In 1977, the process was called the Lead Time Syndrome by Hal Mather and George Plossl, following experience of the US semiconductor industry. It appears that 45 years later, the semiconductor industry is repeating the same cycle.
Semiconductor supply chains
A previous blogpost discussed the shortage of semiconductors for the automotive industry. Since then, it has been reported that semiconductor shortages will affect the availability of most products that rely on electronics. This is the Lead Time Syndrome in action.
Automotive semiconductors are produced on older generation machines which are not interchangeable with later model machines, so capacity is relatively fixed. Total demand from the automotive industry is less than 10 percent of the semiconductor suppliers’ total sales. Hopefully, it is viewed as a separate market segment; however, the input materials are similar.
The potential shortage of semiconductors was first identified in Q2 2020, due to shortages of silicon wafers from the foundries, substrate materials and other discrete components, caused by COVID 19 shutdowns. However, the extent of the problem only came to light in Q4.
The suppliers of semiconductors are Tier 2 or 3 suppliers in an automotive or electronic supply chain, engaged in Assemble, Test and Package (ATP). They supply to Tier 2 component suppliers or Tier 1 suppliers of sub-assemblies. Upstream from semiconductor suppliers are the ‘foundries’, where silicon wafers have circuits etched, then the wafers are cut into chips for ATP. The suppliers at each tier have their suppliers of designs, materials and equipment, which provides for complex and global supply chains for brand companies.
When demand for computer chips was increasing, due to ‘work from home’ directives under COVID 19, the supply of materials was allocated to consumer electronics, given the low level of sales to automotive. When it became evident that the output of vehicles would be limited due to the shortage of semiconductors, brand companies in other sectors took action in their markets by delaying the launch of new products and allocating products to retailers. They also influenced their Tier 1 and 2 suppliers to increase orders for semiconductors – Just in Case!
In normal times, the lead time for a semiconductor order is more than three months. As capacity remains the same, lead times have been increased and the delays will affect the output of finished products. If the orders for semiconductors continue to increase as a reflection of increased lead times, the availability of consumer finished products will be affected until there is a ‘circuit-breaker’ in demand or supply.
For demand, there could be a reduction in consumer interest, as they experience long lead times for deliveries and the inability to negotiate prices or terms. For supply, capacity can be increased through building new foundries and factories, which has commenced with announcements of potential investments in the US and Europe. New capacity could therefore be available in late 2022 onwards, which means another18 months of disruption. However, the effect will only be known after the additional capacity is made available – has demand really increased, or will new capacity remain idle?
Addressing the Lead Time Syndrome (LTS)
While the LTS problem can be described, a systems based ‘solution’ is currently not available, but actions can be taken to ensure that lead times can be met. The three ways to enable lead-times for customers is through available capacity, inventory or reducing time in Operations. To reduce throughput time consider:
- The Theory of Constraints enables planners to identify bottlenecks in operations
- Within each planning slot or bucket the total time (or load) consists of:
- Productive work – the processing time
- Non-productive work, including time for set-up, cleaning and waiting. Single minute exchange of dies (SMED) should be the aim for set-ups. Wait time (for resources to be available) should be another focus for improvement. Manage the overall equipment efficiency (OEE) to have the productive capacity available
To reduce the impact of demand fluctuations, supply chain professionals need to understand their supply network. It is a complex, adaptive systems (CAS) which cannot be ‘managed’, but only analysed to enable a better understanding for possible actions to be taken.