Changing expectations
To allow for ‘Unknowns’ in an economy and to carry a lower risk profile, organisations are likely to make their buying and supply decisions to cover a shorter time horizon and to order in smaller quantities.
The pandemic has changed expectations of what can be achieved in a short period. The most visible example is the speed at which employees have switched to working from home. Instead of the typical many months of planning meetings and implementation, management at a teleco business discussed the working options on a Friday; by Saturday the decision was made for 25,000 staff to work from home and on Monday the change had been made. Also, within 36 hours Asia based call centres were closed and domestic located centres opened. In 10 weeks, more improvements were made to the customer app than in the previous six months.
With each of these changes, there would have been a requirement on suppliers for speed and on-time delivery. Similar changes to process and work practices have occurred in many businesses, so now there are different expectations of what is possible.
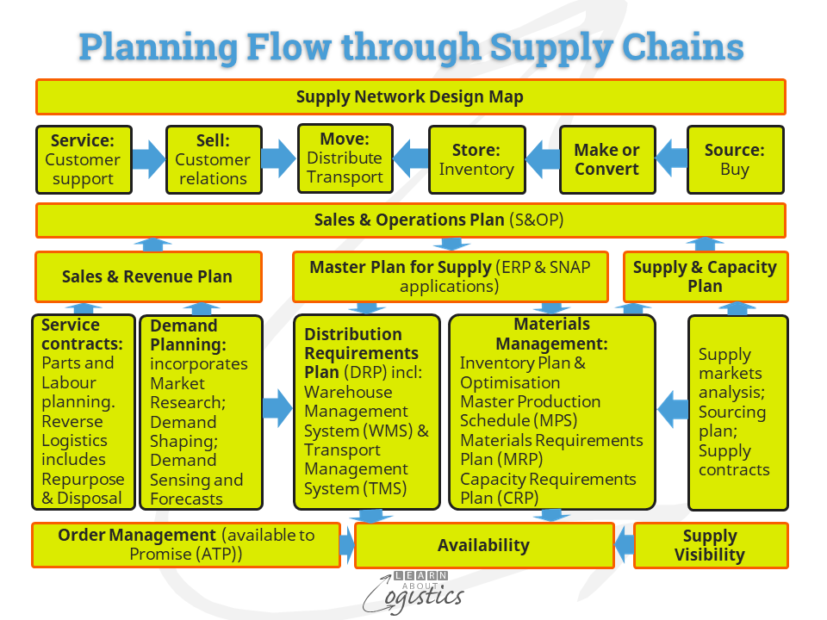
The planning process shown in the diagram holds true for an organisation, whatever the speed of response. For cost effective supply chains, the requirement is stability upstream for planning to satisfy downstream customer orders, or sales forecasts. However, stability of customer orders and forecasts is less likely in the future. A previous blogpost discussed adaptable, agile and flexible supply chains and the actions that a business could take when adapting to the new situation.
For businesses that sell finished product or supply intermediate items for consumer packaged goods (CPG) or fast moving consumer goods (FMCG) industries, the more likely demand patterns could be:
- The traditional inventory techniques of calculating finished goods safety stocks based on a normal demand distribution is limited to only high, consistent and predictable selling products
- Intermittent demand: Due to multiple stock holdings at many retail shelves, rather than a few main and secondary distribution centres
- Lumpy demand: unpredictable demand pattern that does not comply with a normal distribution. The traditional inventory techniques of calculating safety stock based on a normal demand distribution, may not apply
- High service levels for low volume items: Some product lines are considered important, such as new heavily promoted product introductions. A high service level (98 to 99 percent) is expected
- The cycle and safety stock required under intermittent and lumpy demands (a skewed distribution) will be higher than under a normal distribution pattern
- Businesses further up a supply chain find that orders from customers are even less a representation of actual end user demand for the finished product (often due to the ‘Bullwhip Effect’)
To provide speed of response for customers in the diagram above, the Availability must be known, based on the Order Management status and Supply Visibility, linked to Operations Planning. These are (ideally) the inputs to S&OP – Sales and Revenue Plan and the Supply and Capacity Plan, plus the output from S&OP – the Master Plan for Supply. The S&OP cycle is (again ideally) held to 13 x 4 week planning periods per year. This provides a known total capacity for the business over the planned horizon, which must be used to avoid nervousness in the Operations Planning process.
A well known measure to describe the challenge is the P:D ratio: Procurement and Conversion time to the Demand latency time.
Demand latency: The translation of market consumption to an order signal that can be satisfied. The time taken from when an item is sold to a customer until the order for replacement items is processed (adapted from Supply Chain Insights).
Options to reduce the P:D ratio are:
- Improve forecast accuracy – difficult in a time of heightened sales variability. But can improve the quality of market knowledge
- Add safety stock and/or capacity buffers along supply chains. Difficult to achieve outside of your business, especially as the buffers were removed to improve asset utilisation
- Standardise the product range through usage of common parts or ingredients
- Simplify the product range through reduction of SKUs
- Reduce the P time – supplier contract negotiation, production times and lead times through supply chains
The closer that P time is to D time, the less inventory is required to satisfy customer needs, but this is dependent on the accuracy of data. For more than 50 years there have been training workshops that assist people to implement data accuracy through a supply chain – to what benefit?. While RFID and sensor technologies can assist, the situation in too many companies can be that when a customer order is accepted and a delivery date given, the confidence level for success is low.
If data accuracy through supply chains becomes a part of managers’ performance (and bonus) measure, an additional step to assist planners in the current volatile situation is investment in supply chain applications, which are specifically designed for a task.
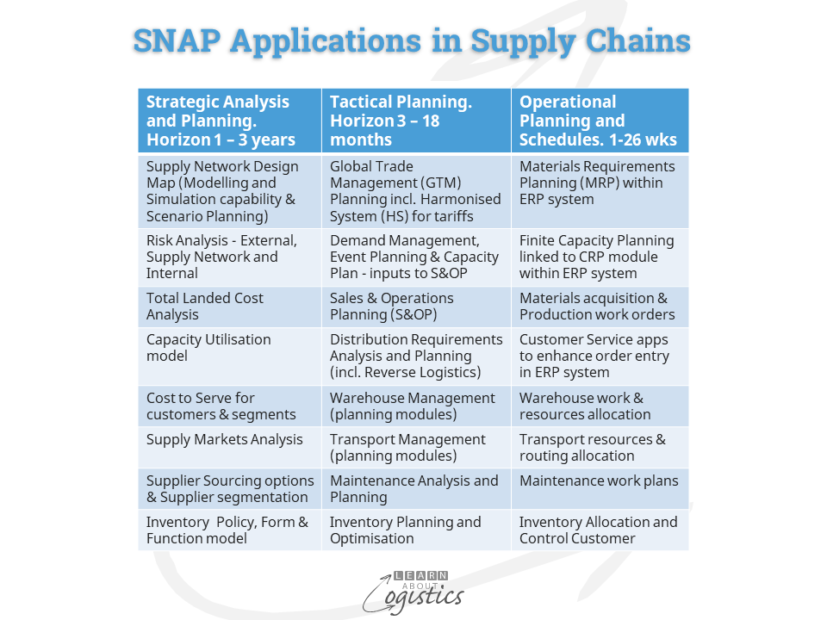
In an ideal situation, an organisation would have an ERP business platform and a Supply Network platform. The latter would contain a selection of the specialist SNAP applications shown in the diagram, enabling Analysis and Planning of an organisation’s supply chains.
As ERP systems hold a dominant position in the IT market, they will not be replaced and are unlikely to change their configuration. However, ERP system can be re-positioned within an organisation to become the transaction backbone of the business. This system would contain an audit trail of sales orders, purchase orders and payments, plus accounting, production and people data and a reporting capability.
The SNAP applications are able access the base data in the ERP backbone and download the required data. Planners then complete the task and upload the solution to the ERP backbone for consolidation and access.
As part of the recovery process from the pandemic, companies and supply chain professionals need to consider the role of Operations Planners and the tools at their disposal to provide accurate and acceptable plans for your organisation.
Please Note: Learn About Logistics is moving premises. The next blogpost will be published on Monday August 10. Thanks for learning with LAL.