Is there enough inventory?
Commentators are writing that post-COVID 19 supply chains will become more adaptable, agile and flexible, but is this a true reflection of what is possible?
The terms are interchangeable and incorporate meanings of ‘willing to change’, ‘versatile’, ‘move quickly and easily’, ‘think and understand quickly’ and ‘well coordinated’. The terms can also be used by management when explaining how their staff rush to respond to every customer’s latest need.
Currently, farmers in Australia are waiting for replacement parts to go into their imported farm equipment and Asian and Indian grocery stores have some empty shelves because re-supply from importers has not arrived. This is not necessarily because of low inventory through a supply chain, just that it is in the wrong place or wrong form.
A table at Supply Chain Insights illustrates the inventory situation in US industrial groups – nine that are ‘Make to Stock’ and two possible ‘Make to Order’ or ‘Assemble to Order’. Between 2004-06 and 2014-19, all groups increased their inventory days of supply; ‘Make to Stock’ has Food up by 10 days through to Beverage up by 76 days. The situation in other parts of the world is unlikely to be different from the US; Logisticians learn from the same textbooks and use the same software.
For cost effective supply chains, the requirement is stability upstream for planning to satisfy downstream customer orders (or sales forecasts). That point in the flow of materials was originally called the Order Penetration Point (OPP), but is now called the Order Decoupling Point or the Demand Penetration Point. Downstream. From the ODP, downstream it is customer orders that control the flow of items; while upstream, the drivers are forecasts and plans. Factors which influence the ODP are demand volume and variability and lead times for supply, production and distribution.
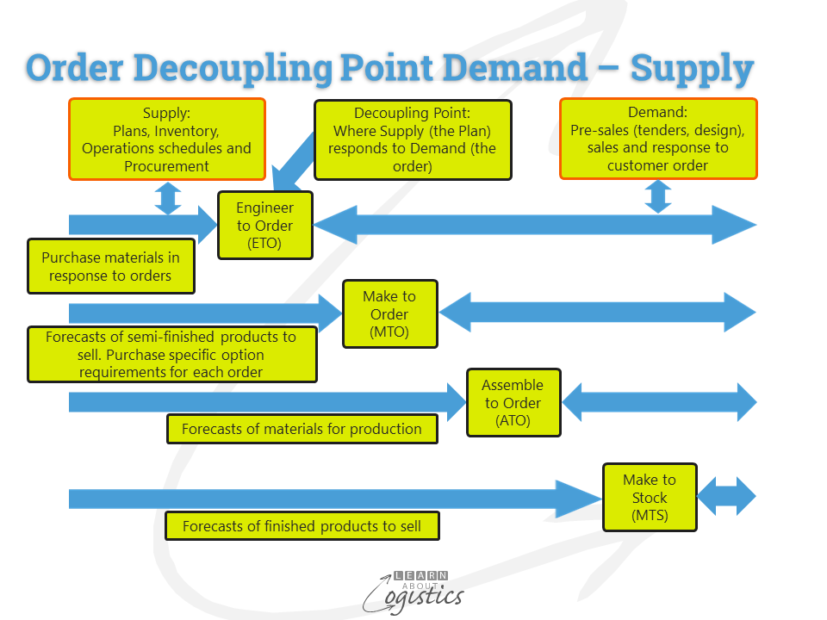
Changing the ODP in a business to enable greater flexibility, requires a range of policy decisions that will influence the structure of supply chains and management of Logistics.
Flexibility in Make to Stock (MTS)
At MTS businesses, the objective is to have finished products available for purchase by customers. A decision by a brand company’s supply chain professionals is therefore the delivery time from order – will inventory be held close to customers, at a geographical location in country that enables quick delivery by truck, or at a regional or global geographical location that requires delivery by sea or air?
The further away that inventory is from a customer, the more that demand variations become critical, requiring attention to inventory buffers, cycle inventory, in-transit inventory (i.e. moving warehouses) and lead times.
The extent of demand variability will govern the level and chase inventory build policy. Level is to hold production level, while inventory fluctuates and Chase is to build inventory with demand increases and falls. Extreme seasonality (say for food products) requires a mix of Level and Chase strategies which also requires a flexible labour force policy:
- employed on an annual flexible hours basis
- employed on a standard work week basis, but in sales downturns can be effective elsewhere in the organisation
- seasonal contract
- casual ‘hire and fire’
So, as inventory is held closer to customers, costs will increase. The greater demand variability is for an item, then inventory should be held further up the supply chain, as work-in-process or raw materials, to be quickly converted. But this requires flexibility in production for a quick response.
As factories become more capital intensive, flexibility can be affected by changeover times for dedicated equipment. In process industries, flexibility can be improved by installing smaller (but more) holding tanks, to enable shorter production runs. To increases flexibility in a discrete business, implement the principle of ‘one minute exchange of dies’ (OMED) for quick changeovers on machines. For lower sales volume products, packaging machines should be purchased for their changeover flexibility, rather than throughput speed.
Increasing the ‘long tail’ of SKUs in MTS businesses appears to have stopped, as major MNCs are reviewing the viability of their supply chains with high SKUs. As an option, MTS businesses could produce their low volume items in separate MTO or ATO facilities, closer to customers. This removes the need for multiple set-ups and short runs on equipment designed for volume based production and distribution. It also means that transport availability risks are reduced for low volume SKUs.
Flexibility in Make or Assemble to Order
Additional flexibility is provided in MTO and ATO operations through ‘Form Postponement’ or ‘Delayed Configuration’. Product lines have a common platform of modules, components and materials that are held in inventory. The product customisation (for MTO) or final assembly (for ATO) only occurs when the customer requirement and/or market destination is known. The benefits of Postponement are:
- Forecast at the generic product level (MTO) or material/component level (ATO) have less volatility than at a MTS product SKU level
- Value of inventory held is reduced – it is held upstream in an unfinished form
- Product variations are created, completed and distributed without finished goods inventory or out of season (fashion) risks
Also, an organisation’s ‘cost to serve’ can be reduced with an MTO or ATO production structure:
- Engagement with customers e.g. improved process quality or co-design of products
- Supplier involvement increased as closer to their customer’s customer
- Quick decisions for flexibility. Reduce organisation layers and review span of control for managers and supervisors. Greater decision responsibilities for staff
- Implement IT applications designed for an ATO and MTO to align operations with market demands
Gaining flexibility in operations is not a short term exercise – there will be a lot of internal selling to do, even with the pressure of the pandemic. Then there is also the work to do in building management and staff capabilities to accept and work in a more flexible environment.