Elements of Supply Planning
Understanding your supply markets, which is called Supply Planning, is one of two critical roles of Procurement. The other is the Purchasing process. The process of Supply Planning was developed in late 1980’s, but it has not become commonly established in organisations – why?
One reason could be that the positioning and process steps of Supply Planning have not been made clear. For a start, in articles and presentations, the term Category Management has been used in preference to Supply Planning and the total implementation has appeared to be complex.
The objective for Supply Planning is to build a competitive supply base that achieves the lowest total cost of ownership and is an integral part of an organisation’s Supply Network. The term Supply Planning addresses a process which contains three separate but linked activities:
- Category Analysis: the allocation of purchased items into categories, with input from the ‘Cost Map’ of expenditures and suppliers
- Spend Analysis: the ‘Risk-Spend Positioning’ matrix is developed from the Risk analysis and the consolidated spend by supplier from the Cost Map. This is also the spend figures in the ‘Supplier’s view of the buyer organisation’ matrix. When the two matrix are linked, they provide the ‘Supplier Capability and Relationships’ guidance for an item or sub-category
- Sourcing Plans, which includes ‘Supply Markets analysis’ and ‘Disposal Plans’
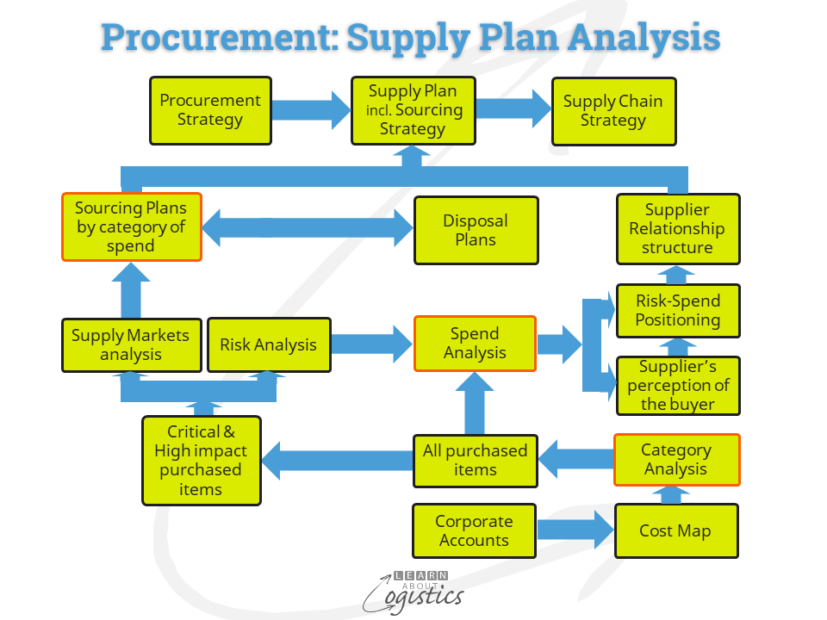
Category Analysis from the Cost Map
This is the process of clustering similar goods into larger potential contracts, which should assist Procurement in lowering the total cost of ownership (TCO) and reducing administration costs. It is a cross-function process, undertaken with the internal users of the category and other groups that can influence the category’s specification and quantity.
The main input to Category Analysis is the Cost Map, generated by corporate Accounts. The diagram shows sales income segmented into the main groups of purchases; however, as this is based on the needs of Finance and Accounting, additional work is required to consolidate supplier accounts for analysis.
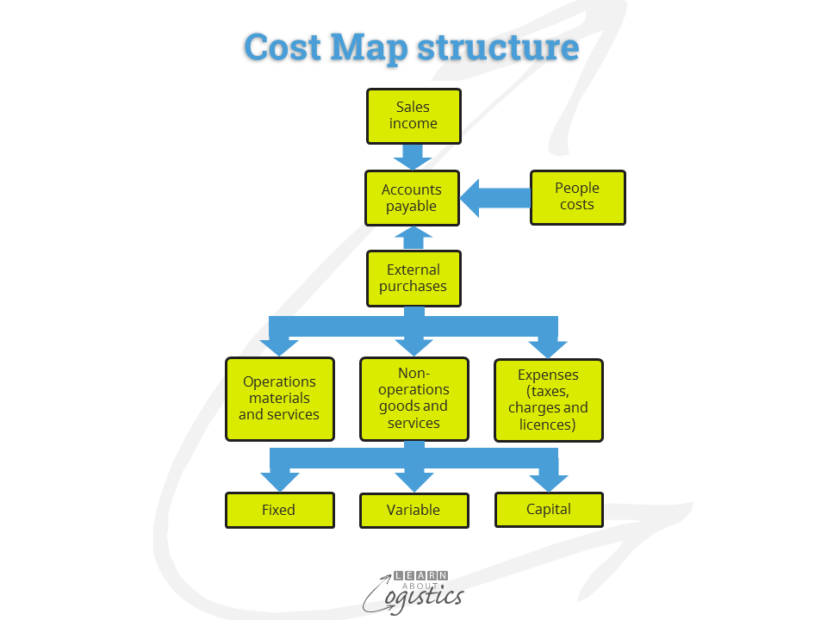
To complete the Category Analysis, the five groups of spend are segmented into clusters of increasing focus (Note that Operations materials and services are also called ‘Direct spend’ and Non-operations goods and services are called ‘Indirect spend’)
The items are initially grouped as either ‘supply industries’ or ‘process technology’. Examples within each group are:
- Supply industries groups: Metals type; Ingredients type; Packaging type etc.
- A supply industries group is named ‘Ingredients type’
- A Category within this group is named ‘Sweeteners’
- One of the sub-categories is named ‘Glucose’
- Process technology groups: IT and telecoms; Logistics services; Travel and entertainment; Facilities etc.
- A process technology group is named ‘Facilities’
- A Category within this group is named ‘Industrial supplies’
- One of the sub-categories is named ‘Safety glasses’
The categories of spend will vary to suit the needs of each organisation. For example, a fluid transfer pumping system will be categorised differently in the health or food industries than in the waste water maintenance industry.
In large engineering based organisations (e.g. mines, power generation and defence contractors), the categorisation process has internationally recognised standards for category formats. These are the United Nations Standard Products and Services Code (UNSPSC) and the NATO coding structure.
Risk Analysis as input to the Spend Analysis
The link between Category Analysis and Spend Analysis is a Risk Analysis. This includes all associated supply risks, such as external markets and process related risks that are defined and where possible, mitigated. The analysis requires that the supply chains of items and sub-categories are documented and understood,
A 2018 blogpost identified the classification of risk factors in an organisation’s Supply Network:
- External risks: arise from interactions between a supply chain and its wider environment
- Supply network risks: within the inbound and outbound supply chains
- Internal (enterprise) risks: related to potential uncertainties in the execution of an organisation’s supply chain strategy
- Supply chain process risks: identify an inability to achieve consistent outcomes relating to planning the movement and storage of materials and resources and deliveries of products or services
- Risks within Procurement
- Risks within Operations Planning (including subsequent Quality and OH&S risks)
- Risks within Logistics
For items in the ‘process technology’ group, a critical Procurement risk factor is the potential financial and reputation impact on the organisation if the buying process goes wrong. For example, in the ‘Marketing’ process technology spend group, examples of potential impacts are:
- high impact: product advertising
- medium impact: market research
- low impact: promotional items (giveaways)
A companion blogpost discussed the three levels of risk in supply chains, which link to the risk classifications listed above:
- Known risks
- Known – unknown risks
- Unknown – unknown risks
The completed Risk Analysis is applied to the ‘Risk – Spend’ analysis. The ‘Cost Map’ provides the consolidated spend figures.
Decisions concerning responsibilities, authority and accountability in Procurement depend on the size and complexity of your organisation. This includes how responsibility is allocated for the items and sub-categories and their sourcing plans. For a multi-national business, an approach could be:
- High impact items: centralised, global sourcing; a complete sourcing plan, with an horizon of three to five years
- Medium impact items: regional sourcing; an abridged sourcing plan for the next 12-18 months and
- Low impact items: country sourcing, requiring a tactical negotiating plan
The selected approach will have an influence on the Supplier Relationship structure defined in the Spend Analysis and based on the Risk – Spend positioning and ‘Supplier’s view of the buyer’ for an item or sub-category.
Each of the Supplier Relationship structures will have a methodology or process for:
- selecting and prioritising improvement projects
- forming cross-functional teams (where required)
- managing supply market intelligence and information gathering
- ongoing risk analysis
- workflow processes, with built-in flexibility to allow for judgement by supply category specialists
The Sourcing Plans for items and sub-categories are developed from the Supply Market analysis and Disposal Plans. These will be discussed in the next blogpost.
The Supply Plans, which become part of the Procurement Strategy, combine the ‘Sourcing Plans’ for physical items and the the people based ‘Supplier Relationship’, This allows Procurement professionals to more effectively structure the ‘best’ deals with selected and known suppliers.