One Plan for your Supply Chains
The previous blogpost discussed how uncertainty and disruptions in supply chains are likely to be experienced for the foreseeable future. Reacting to events by ‘putting out fires’ looks good as a ‘can do’ attitude to impress others, but is an ineffective and expensive way to operate.
As an alternative, your business can build a planning regime with Sales & Operations Planning (S&OP) as the tactical planning ‘hub’ of the business. But just having a tactical plan is insufficient – there needs to be a ‘One Plan’ process for your business. This process links the strategic, tactical and operational planning stages and utilizes the same data set, but with different levels of granularity.
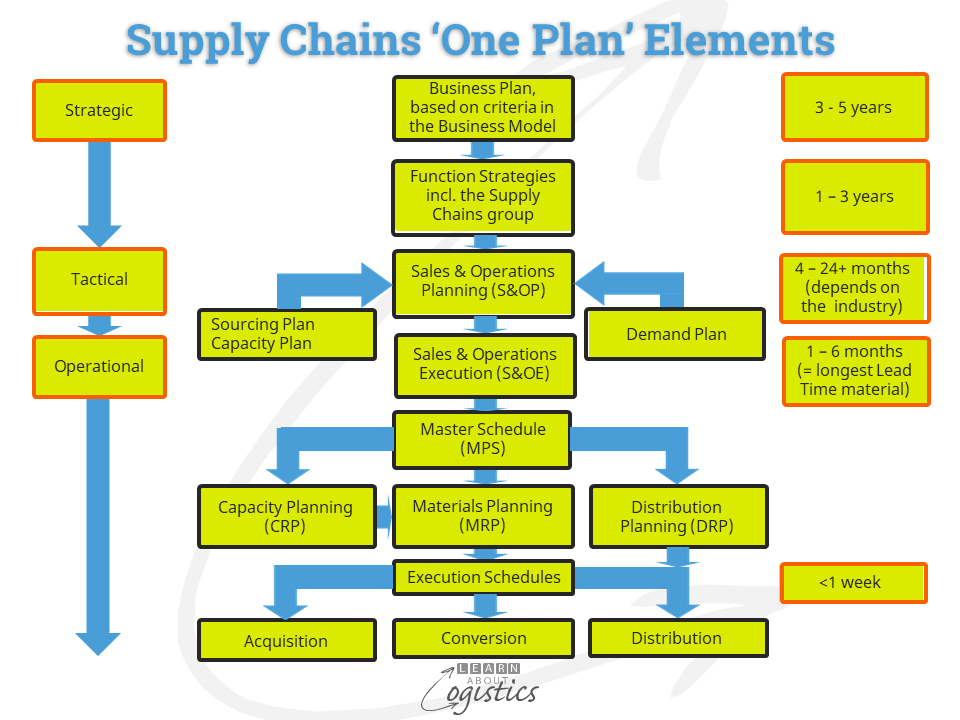
Your ‘One Plan’ will have five elements as shown in the diagram:
- Business Plan: for directing the future of the business. This Plan is strategic and ‘owned’ by the senior management team
- Function strategies e.g. Procurement, Logistics
- Sales & Operations Plan (S&OP): the methodology balances the actual and forecast demand for products with the available supply, resources and capacity. The S&OP output is ‘owned’ by the senior management team, but the process is managed by the Supply Chains group
- Sales & Operations Execution (S&OE): takes outputs from the S&OP to plan availability of stock keeping units (SKU), using materials, capacity and distribution planning tools. The process is owned by the Supply Chains group and managed by Operations Planning
- Execution Schedules: defines the order in which operational activities of materials acquisition, materials conversion and product distribution will occur. The process is managed by Operations Planning, but the activity may be done within operational departments e.g. distribution
To have ‘buy-in’ from all functions and an understanding of output decisions requires affected divisions, groups, functions and departments to be involved and provide input at each stage of the ‘One Plan’ process.
The flow of planning your Supply Chains
The Business Plan is developed from criteria provided in the Business Model. This is the ‘why and how’ structure of your organisation, selected and approved by the owners or shareholders for achieving the overall goal and objectives. The Business Model provides guidance to the senior executive team and identifies:
- how the enterprise manages its markets,
- how responsibility for sales and profit is structured,
- customer segments focus,
- types of product and services to be sold and how they are differentiated from competitors,
- internal and outsourced functions,
- sources and collection of revenue and
- how the enterprise is financed (e.g. borrowing limits)
The Business Plan provides the direction for taking advantage of longer-term opportunities and is the basis for subsequent decisions and actions. The Plan enables management to make informed choices concerning the ‘best’ portfolio of products and countries (or regions within counties) where the business operates and the steps required to gain market share or increase profit margins.
Function strategies are developed based on the direction and framework of the Business Plan. The Supply Chains strategy is consolidated from each function strategy – Procurement, Operations Planning and Logistics.
The Sales & Operations Plan (S&OP) is the tactical planning ‘hub’ for an organisation; it balances demands from customers with the materials, resources and capacity available, As the S&OP process facilitates a change in the way the organisation works, implementing S&OP relies on the ability of people to work as a team rather than individual departments. The performance measurements of the management team therefore need to be aligned, to enhance co-operation – we behave how we are measured.
The Sales & Operations Execution (S&OE) process plans for individual SKUs to be available for customers. The approved S&OP for the forward planning period is the primary input for S&OE. To provide some stability in the planning process, there should be a ‘freeze period’ in which the current operational schedules can only be changed by authorisation of senior management. The planning period for S&OE is therefore from the end of the ‘freeze period’ to the planning horizon (the longest lead time of inbound materials).
The diagram shows S&OE applications used in a manufacturing business – the Master Schedule, Materials Requirements Plan (MRP), Capacity Requirements Plan (CRP) and Distribution Requirements Plan (DRP). While each organisation’s planning requirements have similar needs (inputs, capacity and distribution), the software applications used to assist this may carry different names.
The Master Schedule plans the aggregate output from Operations to meet the order requirements from Sales and customers; this provides some level of stability for material acquisition, conversion (production) and distribution. The Master Schedule provides the inputs that drive the MRP, CRP and DRP schedules.
The Execution Schedules use outputs from MRP to establish the acquisition schedule for materials (especially for imports), components and products. For Conversion and Distribution, if ‘demand-pull’ (i.e. just in time) techniques are used, Kanban (pull) signals will replace the schedule. If demand-pull is not used, schedules will identify the order in which input items will be converted to output products and the order of loading vehicles and moving inventory items.
The Execution Schedules can be performed as part of a 3PL service, but the S&OP and S&OE planning should remain as intellectual property of your organisation.
To assist customers with understanding the capability of your business to service their requirements, the S&OE process can provide Customer Service with information concerning product availability and lead times:
- Available in Stock (AIS)
- the item is available for delivery within a defined geographic area
- Available to Promise (ATP)
- the item is scheduled within the current production or import planning period
- Capable to Promise (CTP)
- the product can be planned if there is sufficient demand
- product, components or materials are available within a defined lead time
- there is available production or storage capacity and capability
- Capable to Deliver (CTD)
- the following are known and acceptable for planning a product, if required
- transport mode, capacity and schedules
- transport nodes – capacity and schedules
- transport lead time and variability
- the following are known and acceptable for planning a product, if required
In an ideal Supply Chain flow environment, the S&OE plan is provided to Tier 1 suppliers for input to their S&OP process and those suppliers will do the same for their Tier 1 suppliers and so on. This is how visibility and trust in supply chains is enhanced. When this occurs, Uncertainty is reduced, allowing organisations along the supply chains an opportunity to become more effective rather than reacting to events.