Planning concerns have not changed
Management has limited time to consider the strategic and tactical direction of your organisation. Also consider the amount, detail and accuracy of data and information required, as it flows through your organisation. At each level of the information flow, there is a need for alignment between the management’s time available and the volume of data to be considered – the decision horizon.
The discussion about which horizon to be used at each level in Planning and Scheduling has occurred over a long period of time. The cartoon below is taken from the book Statistical Forecasting for Inventory Control by Robert Brown, published in 1959 – well before the general use of computers.
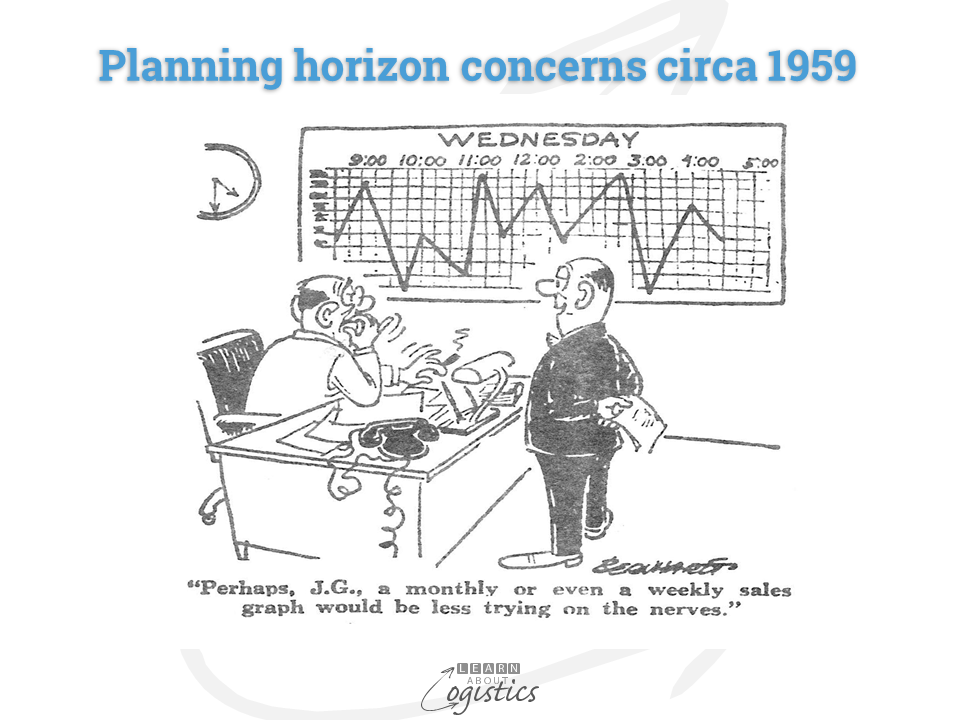
When facilitating supply chains, Planning mainly concerns people and their willingness to collaborate (which starts with co-operation, then co-ordination). This enables a common visibility into the future; to identify and agree about outcomes. Software applications can assist, but if collaboration is not forthcoming then technology will not help. However, Scheduling is concerned with the detailed execution of plans and therefore can be helped by using software applications and maybe the magic of AI/ML.
Horizons at each level in the process flow
The diagram below shows that both Planning and Scheduling of supply chains should be contained within the ‘One Plan’ approach. This requires that all groups work from the same base data, to achieve the desired outcomes. However, the data and information has a different granularity, depending on the stage in the process flow.
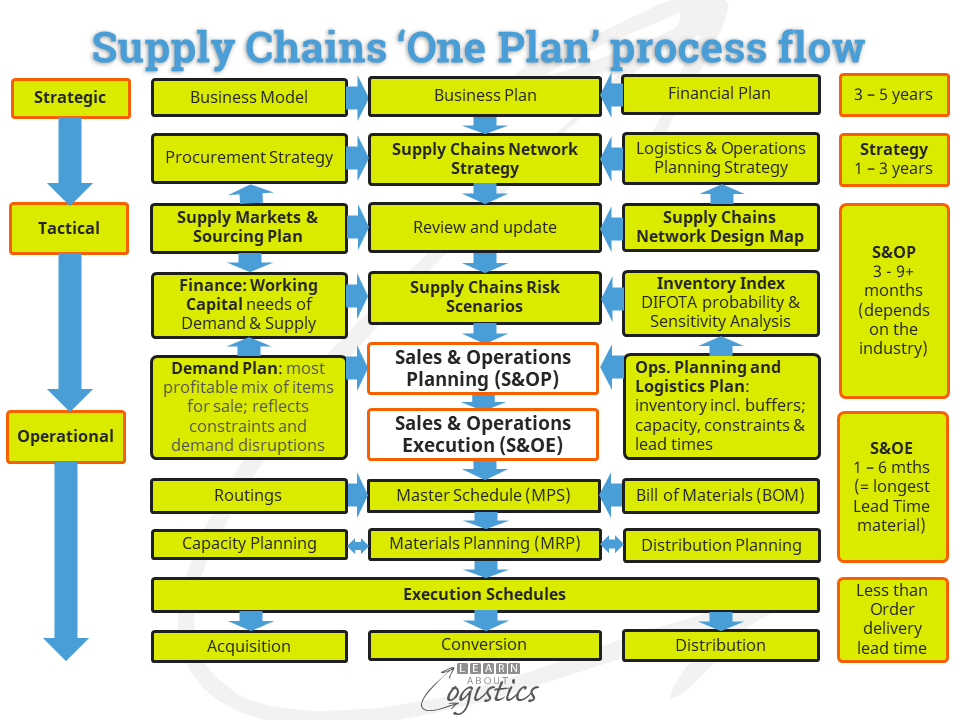
On the right side of the diagram is shown the typical horizon for decisions at the Strategic, Tactical and Operational/Execution stages in the Supply Chains process flow. At the Strategic stage, the Supply Chains Network Strategy is the amalgam of three separate strategies – Procurement, Operations Planning and Logistics, with input from the Business Plan. The strategies are in place for between one and three years, but could be longer. Time, data and information are therefore considered at the macro level.
At the Tactical stage, the key decision element is Sales & Operations Planning (S&OP), with an horizon of between three and nine months. The horizon can extend further, depending on the industry. For example, in businesses that use seasonal commodities, the S&OP horizon could extend to 18 months, enabling estimates of intended purchases of each commodity. The estimates are the basis for buying contracts on the commodity’s Futures Exchange, which provides an indication of future input cost to the business.
The S&OP process commences at month three, because the current and following month (at least) are scheduled in greater detail through the Sales & Operation Execution (S&OE) process. Under S&OE, Operational schedules have their horizon as the longest lead time across the purchased items; typically between one and six months. The horizon for Execution schedules is the lead time for current customer orders.
Data inputs for the ‘one plan’ process
At the Tactical level, data gathering for Procurement is through Supply Markets Intelligence; gaining an understanding of global supply markets for the main and/or critical inputs. Based on the data, the potential supply risks are identified and the gathered data distilled into the Supply Markets Plan. For Operations Planning and Logistics, the main input is the Supply Chains Network Map. This describes all the elements that interlink to enable the Network to function and therefore highlights where potential risks may exist.
These respective functional Plans are structured using large time blocks (half year and quarters), with macro data and information. They are regularly updated to reflect changes and to update the Supply Chains Risk Scenarios.
Additional inputs to the Scenarios are the the Working Capital needs to support projected Demand and Supply requirements and the Inventory Index. This is the probability measure of the organisation’s capability to ‘Deliver in Full, on Time, with Accuracy (DIFOTA) and Sensitivity Analysis, to assess how the probability (of the variable) in each element is affected by changes in the probabilities (variables) in the other elements.
The hub’ of your business is the S&OP. developed with data and information from five direct inputs shown in the diagram, which can be Supply Network Analysis and Planning (SNAP) applications:
- Working Capital requirements and the Cash to Cash Cycle, provided by Finance
- Inventory Index – the capability of delivery to customers (DIFOTA and Sensitivity Analysis)
- :Supply Chains Risk Scenarios, with input from
- Supply Markets & Sourcing Plan using inputs from Supply Markets Intelligence Analysis and Sourcing Plan
- Supply Chains Network Design Map
- Demand Plan including sales forecasts consolidated to product ‘families’. Incorporates Demand Sensing and Demand Shaping
- Logistics and Operations Planning Plan – inventory (by location, identifying form and function) by product ‘family’; capacity constraints and lead times
The S&OP process cycle is typically monthly. However, to obtain consistency between the measurements, consider 13 x 4 week periods per year. At the Tactical level, Planning must measure intended outputs against the main capacity constraints in Operations, Therefore, all SKUs are standardised to an output measure and grouped together into ‘families’ that use the particular constraint. Strategic Business Units (SBU) that undertake S&OP, must use standard definitions and a standard approach, to ensure the numbers mean the same throughout the organisation.
At the Scheduling level, the horizons are shortened to reflect the more detailed requirements. The S&OP output is converted to the S&OE SKU inputs, which commences at the Master Schedule (or similar term) in the corporate ERP system. The Master Schedule is the driver for schedules concerning inbound supplier items, production and deliveries. With the horizon as the longest lead time of a material in the Bills of Material, the Master Schedule is calculated on a monthly basis for months two and three, then quarterly thereafter. For the Execution Schedules, the horizon is shorter again, at the Order delivery lead time and therefore uses more data and information.
As more detail is used, so is the need for software tools. For Planning, concentrate on people and process, as these are the challenge in making your Strategies and Tactical S&OP effective. Easy to use ‘what if’ software is a ‘nice to have’. For Scheduling look to technology tools that can assist the process.