Salaries and skills
Since the term Supply Chains appeared, education, recruitment agencies and industry executives have debated the knowledge and skills that Procurement, Operations Planning and Logistics professionals should be able to discuss and demonstrate.
Recently, Bastian Consulting, an Australian specialist supply chain recruitment firm, reported that it surveyed more than 500 supply chain executives in the Asia Pacific region (Australia, New Zealand, Singapore, Malaysia, Hong Kong, Japan and Thailand) for an update concerning senior supply chain appointments.
The question concerning salary provided a range (in US dollars) across the region:
Director level:
- Supply Chains U$172k-269k
- Procurement U$179k-246k
- Logistics Operations U$134k-187k
Manager level:
- Supply Chains U$97k-123k
- Manufacturing U$75k-97k
The executives were questioned about the skills required (what a person can do):
- Technical skills: Inventory Management is the most sought technical skill, followed by ‘best practice’, project management and risk management
- Technology skills: ‘expertise’ (not defined) in Artificial Intelligence (AI), Industrial Internet of Things (IIoT), robotics and data analytics
- Soft skills: the ability to communicate effectively and collaboration with others are key employability skills
The executives observed a lack of both technical and soft skills when recruiting people for senior roles across the region. This could be due to the structure of degree and diploma programs related to the disciplines, the number of people working in supply chains with qualifications from other disciplines and the limited range of ‘upskill’ courses available. Much of the knowledge and skills are attained ‘on the job’ and therefore depend on the capability of individual employers.
This is illustrated by the requirement that Inventory Management is the most sought technical skill. It is similar to stating that a doctor should know how the human body works – it is assumed. But in supply chains, Inventory Management knowledge and skills cannot be assumed.
Technical skills
The current disruptions to supply chains illustrate that it is critical to define an inventory buffer (capacity buffers have often been eliminated through ‘efficiency’ programs) that provides a level of protection against demand and supply volatility.
For senior roles, inventory skills should be to provide input for the policy and planning framework. This requires knowledge of the Sales & Operations Planning process (or Response Planning as discussed in a previous blogpost) as the forum in which the role of inventory and capacity to balance demand and supply in the business is evaluated by senior executives.
Within production of the framework for inventory, executives and managers require an understanding of policy decisions that can influence the level of inventory required to support the business. Examples are:
- Postponement (if possible) at stages in the production/assembly process prior to products becoming market or customer specific
- Rationalisation of product lines and stock keeping units (SKUs), especially slow and obsolete (SLOB) products. Rationalising the ‘long tail’ of low selling SKUs (through product line extensions) as will raise objections from Marketing
- Design and plan each supply chain, based on their inventory flows, variability, marketing and sales tactics. Allocate locations for inventory
- Use the Coefficient of Variation (CoV) to identify the variability of demand for SKUs and preferred inventory locations based on the pattern of demand
- Establish ‘safety stock’ parameters based on customer demand and variability. Incorporate the ‘lead-time syndrome’ response to unexpected demand
- Calculate the ‘total cost of ownership’ (TCO) for purchased items as the basis of Sourcing decisions
The fourth skill in the list is risk management. Experiences of the last eighteen months highlight that identifying and managing risk is a critical role for a senior executive in supply chains. As discussed in previous blogposts, Uncertainty has increased through supply chains over the past 30 years, as more businesses took advantage of global supply and demand markets. To bring some order and understanding to the uncertainties requires a risk management approach that evaluates possible external and internal disruptions, the likelihood of a disruption occurring, the consequences and identifying actions to mitigate the effects.
Project management is a skill that comes to the fore when implementing computer applications for supply chains or building new warehouses and distribution centres. Even though facilities will be built by developers and builders, it is preferable for logistics executives to have gained knowledge (and maybe a qualification) concerning project management and so be able to ‘speak the language’.
The second skill identified is ‘Best Practice’. It is however, best to avoid this term. Too often, it means copying what other businesses are doing without understanding the ‘why’. In previous times, the saying was ‘you never get fired for buying IBM’, meaning that you were safe in your job if you did what others were doing. The saying remains the same today, only the named company has changed.
Rather than best practice, it is preferable for a person to know how the ‘right practice’ should be identified and implemented for a business. A suggested process to follow is shown in the diagram below; importantly, the five documents required for Supply Chains Network design. The outcome (the right practice) for your business could be different than other businesses in the same industry.
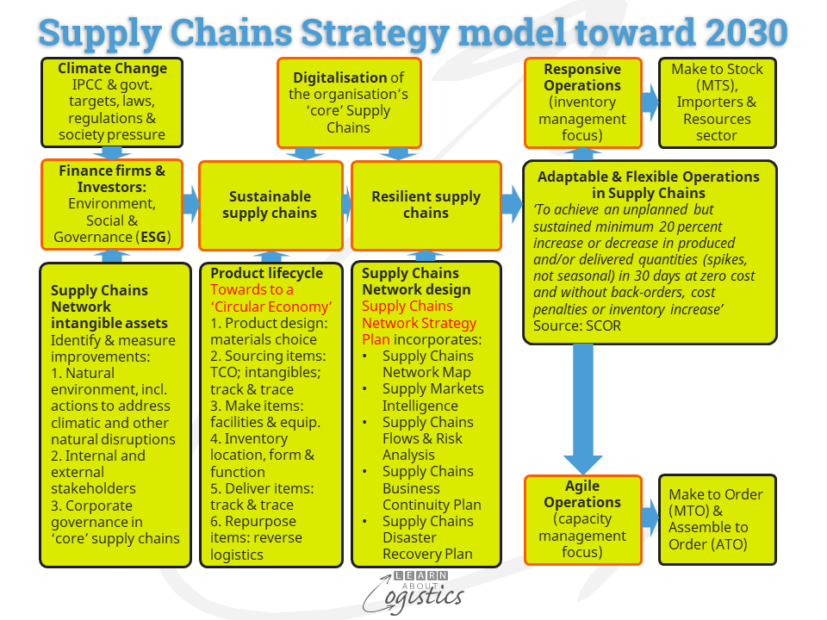
Technology and Soft skills
Technology ‘skills’ should not be at the ‘bits and bytes’ level for executive roles. Instead, they need to have the ability to:
- build a business case for acquisition of the needed technology, using a capital expenditure (CAPEX) proposal
- confidently argue the value of the proposal before their peers
- structure a user requirements specification for Procurement to provide prospective suppliers and
- evaluate proposals from suppliers through structured and knowledgeable questioning
For Soft skills, in addition to the communication and collaboration skills identified in the survey, an additional skill is the ability to ‘sell’ to the executive team in the business. As discussed, there is the need to ‘sell’ technology proposals, but also to ‘sell’ and gain acceptance concerning the concept of supply chains and the scope of Procurement, Operations Planning and Logistics disciplines within supply chains.
For example, Finance, which carries much weight in decisions, considers inventory as a waste and a cost to be avoided. To change this ‘cost down’ attitude is a major challenge for supply chain professionals. It requires an ability to speak the language of Finance and to ‘sell’ this major change to accepted wisdom.
It is beneficial that a recruiting firm has provided a current overview of requirements for senior supply chain roles in the Asia Pacific region. The requirements for other geographic areas could well be different, but this list is a good starting point to review your capabilities for management and executive positions.