Waste happens
When waste is discussed, it typically refers to waste generated within a business. However, an increasing requirement for Sustainability of organisations means that the waste of time and materials must include that occurring throughout the supply chains.
The extent of the challenge can be assumed to be large, but is dependent on the industry sector and the strategies of individual businesses. Waste mainly occurs because of over-production, product damage, spoilage and returns. Over-production can be driven by ‘Just in Case’ inventory policies in seasonal and fashion type industries, while expiry (use-by) dates influence inventory policies in food and pharmaceutical operations.
Minimising wastes
Since earliest times that people have been organised to produce and distribute things, there have been initiatives to reduce waste of time and materials. The most recent of note is the Toyota Production System (TPS) – the forerunner of ‘Just in Time’ and ‘Lean’. It identifies seven wastes within organisations, of which much has been written: Over-production, Inventory, Transport, Process (layout), Motion, Waiting and Defects.
For a better chance of success, the improvement process must include Management by Walking Around (MBWA). This has managers walking their area to talk with and challenge their staff (ask ‘why’ five times) about the:
- Flow of materials, parts and products and associated data and information
- Equipment changeover and set-up process to reduce time
- Workplace layout and housekeeping
Purchased materials must be analysed within the Supply Chains Network Design structure, as a risk reduction process to ask the:
- origin and location of materials and at further processing
- waste generated at each Node in the supply chains
- risks associated with the waste – the likelihood of action (by whom) against the waste and the potential consequences for the business
- possible solutions and profitable markets for treated waste and
- how achievement will be measured
But minimising waste is now a challenge for your organisation’s supply chains. Here, waste is the inefficiencies and excesses during the delivery and storage of goods and services through a supply chain. There are similarities and additions to the seven wastes listed above:
- Overproduction: when more products are produced than necessary, leading to excess inventory and associated waste. Implement tactical operations planning (Sales & Operations Planning) to reduce overproduction
- Excess Inventory: requires additional storage space and working capital. A current example is reported in the Financial Times that Chinese manufacturers are exporting more electric vehicles (EVs) to Europe than they can sell, which has led to thousands parked at port facilities, some for more than a year.
- Unnecessary Packaging: reduce waste by minimizing packaging and use recyclable materials
- Time in warehouse operations: consolidating orders and loading trucks
- Transport challenges: planning, scheduling and routing of transport modes; communication between production and logistics schedulers; processing of orders and delivery instructions
To reduce waste and improve operations the steps are: eliminate, standardise, simplify, combine, integrate. Track the waste back through supply chains to identify the root cause(s) for elimination – ask the question ‘if it were not for what, could this be eliminated?’ Utilise people in the planning/scheduling office, warehouse and trucks to identify and propose solutions for waste with resources and excess spending.
Reverse Logistics activities
With increased responsibility for wastes through the supply chains, Logistics needs to establish Reverse Logistics as an integral part of operations. These are the activities required by the business and 3PLs to efficiently bring items from their current location, through the same or a different supply chain. Reverse Logistics terms start with ‘re’ and the diagram identifies the categories:
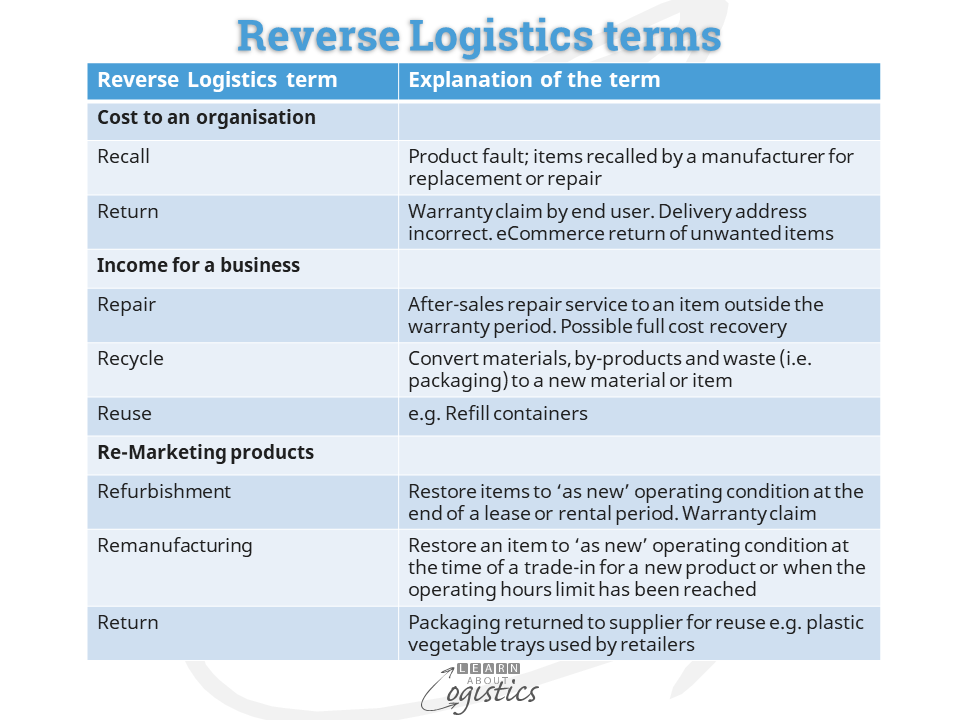
Cost to the organisation – caused by errors in product design, manufacturing activities or Logistics.
- Recall of a product line may not occur very often, but when it does, the costs can be high. It involves quickly identifying the item locations, organising the logistics activities for the recall and then storage of the recalled items, prior to decisions concerning rectification of the problem.
- Return of products may either fit a pattern or be ad-hoc. The cause(s) must be analysed, because if the underlying cause is not identified, costs can escalate
- Logistics processes for product Recall and Return must be reviewed at regular intervals to identify improvements. A mock exercise for a product recall is valid, due to the various departments and disciplines involved
Income for a business: For repairs out of Warranty, the Logistics process is the same as Warranty returns, except that the consumer/customer is likely to be charged for the repair costs.
- Consumer goods (identified as ‘white goods’ – electrical goods used in the kitchen or ‘brown goods’ – electronic and electrical goods used elsewhere in the house) and motor vehicles are typically taken by the consumer to a repair centre, operated by the brand company or an authorised repairer.
- Industrial products typically require on-site servicing and repairs. Depending on the urgency, repairs may be undertaken on any day and at any time. Planning and scheduling is therefore critical to ensure skilled technicians are availability and the location, availability and tracking of service parts. For inventory planning, know how often parts fail (called the Mean Time Between Failure (MTBF)) and for what reason.
- The Logistics challenge is that products are usually under continuous improvement. Parts within a model range can change over time and manufactured by suppliers located anywhere. Tracking of parts by serial number is therefore critical.
Recycling is to convert materials, by-products and waste into new items. Identify materials that can be profitably used in other forms and how to manage their movement and storage.
Re-marketing products is the term used for restoring items for further use.
- Refurbishment and Re-manufacturing. Items that are leased or hired can be re-furbished to enable further use. Items are Re-manufactured when a product is traded-in by an end user or have reached an operating hours limit. Both approaches require a Reverse Logistics and operations process that is managed as a profit centre.
- Returns can be profitable when a commercial buyer works with suppliers to identify how protective packaging can be returned and re-used. If volumes are sufficient, the return is priced into the delivery costs, with savings in packaging material costs.
Identifying reductions in wastes will be an on-going process for the Supply Chains group (Procurement, Operations Planning and Logistics). And change takes time to implement. Reducing wastes will also occur as organisations move their thinking to incorporate supply chains and networks, then value chains that include both demand and supply chains.