Inventory for dependent items
The role of Inventory is to provide a buffer that recognises variability in demand for items and the lead times required to meet those demands. Variability in supply and its lead times is also a factor, due to disruptions through supply chains.
The disruptions in supply chains are likely to continue, especially with the influence of events associated with climate change. The World Metrological Organisation has recently brought forward the 1.5C increase in temperature to 2025, so increased adverse weather events will occur that affect supply chains.
In times past, items purchased for conversion in production were considered as ‘dependent items’. That is, in the Materials Requirements Planning (MRP) logic, the amount of materials ordered reflected expected sales for the finished item, multiplied by the quantities of materials required in the Bill of Material (BOM), less the inventory held and planned to be used over the lead time for the supply item.
A new situation for supply items
Some dependent items are now experiencing a more ‘independent’ demand pattern. That is, due to disruptive events in their supply chains, the demands are independent of the MRP calculation. Inventory management of supply items and especially critical items, must now be part of your organisation’s inventory strategy.
In addition to the inventory calculated through the MRP process, the ‘independent’ demand inventory held in excess of the planned requirements are:
- Fluctuation inventory is inventory held in excess of the calculated cycle inventory and compensates for uncertainty associated with unplanned events. This is usually referred to as either safety stock, reserve stock or buffer stock. Safety stock can be reduced if the inbound lead time is reduced. Shorter lead times can reduce uncertainty, so finished product demand and material use is planned over a shorter horizon and supply can occur at shorter intervals.
For critical and other selected materials, the purchase order or contract call-up and date is the demand signal. The variances are in the quantities received against the order and actual lead time against planned. The calculated standard deviation provides the safety stock for an 84 percent service level. The Positive Z Chart provides the safety factor to apply against the standard deviation for higher service levels.
An alternative to holding safety stock is to plan for safety capacity and safety labour. But this will require additional equipment capacity and/or trained labour to be available. Given the amount of outsourcing and focus on minimising assets, improved management of inventory is a more likely option for Logisticians.
For imported finished goods, an additional safety factor is the uplift applied to the standard deviation of lead time – when the quoted delivery lead time exceeds the order interval. The uplift recognises that In this time period, actual demand could differ from that forecast. The standard deviation of the lead time is multiplied by the uplift when the interval between placing an order is one period and the quoted lead time period is:
- 2, the uplift = 1.63
- 3, the uplift = 2.36
- 4, the uplift = 2.64
2. In-transit or transport inventory, also referred to as the ‘floating warehouse’. Prior to the COVID induced transport disruptions, the variance of supply items purchased by the principal company and the variance of shipping time were low. The inventory could be designated (and planned) as in-transit inventory within the total inventory plan. However, the uncertainty associated with shipping disruptions has reduced the effectiveness of this approach.
3. Anticipation inventory occurs when inventory of finished goods is built in advance of a peak demand and materials are purchased and held for the peak demand. The inventory is used for seasonal demand; public and religious holidays or against potential shortages caused by the planned shutdown of a factory for maintenance, extended holiday periods or supplies of a material becoming restricted.
4. Hedging inventory applies to businesses that use traded commodities, such as natural fibres, grains and metals and reduces the purchase price risk of fluctuating commodity prices. Instead of investing early in physical items, a business can ‘lock in’ the future price of the material through trading contracts against future purchases on international commodity exchanges.
Service parts
Service parts are either for sale to customers as part of the business (mainly in the automotive, defence and industrial equipment industries), or used within a company’s own facilities as service parts for operational equipment. For example, a large mine site may hold over 30 000 different service parts, requiring the inventory and purchasing review of more than 100 part numbers per day!
Planning service parts inventory is based on segmenting the list of parts on the basis of Criticality of each part, as shown in the diagram below. With each service part allocated to its Category, the planned inventory is calculated when the service level multiplier is applied to the standard deviation. For the more critical parts, an additional consideration applied to inventory is the Mean Time Between Failure (MTBF) calculated by the technical staff.
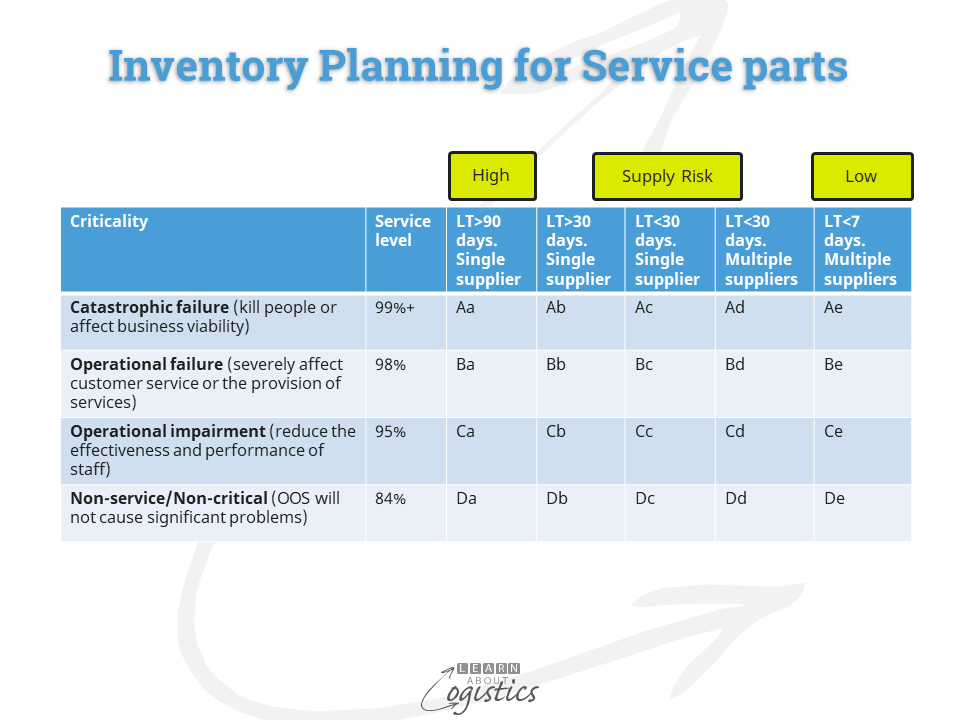
Service parts can also be held as ‘insurance parts’ to ensure their availability for the economic life after the main product is discontinued. These parts are often held in inventory as higher assemblies, such as a full gearbox rather than each of the components. Insurance parts inventory is called ‘life of type’ (LOT) or ‘all time buy’ (ATB).
Service parts for sale can remain in inventory for extended periods before a sale occurs. Logistics professionals must therefore know whether holding the part is earning a return for the business. The calculation is the ‘gross margin return on inventory investment’ (GMROII), calculated as: Gross margin x Inventory turns/1 – Gross margin. Given the costs associated with holding inventory, a business should expect to earn up to three dollars for each dollar invested in service parts inventory.
This discussion about supply items and finished products in the previous blogpost, illustrates that inventory management – policy, planning and performance/control has a structured approach that is fundamental to the role of a Logistician and will be vital for businesses in the future.