Few years remain to make climate change decisions
Success and failures in responses by governments and business to the COVID-19 pandemic has been a learning exercise for all. These lessons will be useful concerning the disruptions that are likely to occur due to climate change.
In 2019, the Intergovernmental Panel on Climate Change ()IPCC) stated in its report “limiting global warming to an increase of 1.5 degrees C would require…global net human-caused emissions of carbon dioxide (CO2) to fall by about 45 percent from 2010 levels by 2030, reaching ‘net zero’ around 2050”. Doing nothing is a policy choice, but will be costly for an economy and its businesses.
For businesses, climate change starts with money. Investors, banks and insurance companies are now requiring measures of environmental, social and corporate governance (ESG) to better determine the likely future financial performance of a business. This has initially affected high emissions industries that are required to take action to reduce emissions (i.e. mitigation). ESG requirements are now likely to cover businesses in fast moving consumer goods (FMCG) and consumer packaged goods (CPG – those with ‘use-by’ dates on packaging),. They will need to reduce their vulnerability to the effects of climate change through adaptation.
As financial and society pressure is placed on MNCs, it will be passed to their tier 1 suppliers, who will then require similar behaviours from the tier 2 suppliers and so on. Those business which engage in ‘greenwashing’ – presenting a grandiose announcement concerning sustainability, but doing very little to implement the ‘strategy’ are likely to receive less funding.
Sustainable and Resilient policies for your organisation’s supply chains
Policy choices require an understanding of the supply chain risks from climate change. The diagram provides a model of the required steps to build this understanding.
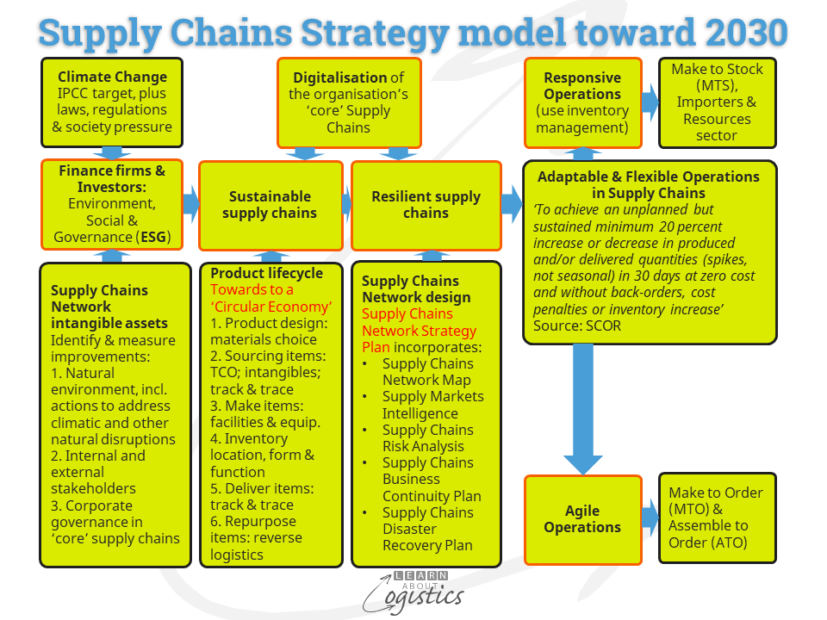
Due to the publicity surrounding carbon emissions, climate change may only be viewed in terms of emissions. Whilst important, emissions are but one factor in the use of resources across all supply chains – clean air and water can have implications for resource requirements.
Sustainable: to identify the potential vulnerability of its supply chains, an organisation’s ESG report is likely to address:
- Design: policies to reduce or eliminate the use of scarce materials; conflict materials and items that encourage bad practices e.g. forest clearing
- Source: policies re buying from countries or areas under threat from natural disasters; low cost country sourcing (LCCS); reduction of travel distances e.g. food miles and congestion costs; reduction of energy and water consumption through each supply chain
- Make: location of known nodes in the supply chains network; critical (owned and leased) facilities and equipment; toxic materials, effluents, waste and disposal at each node; source of energy at each node; elimination of child and exploited labour at each node and link in each supply chains
- Deliver: policies to reduce the climate effects from distribution; channels of distribution used and delivery design e.g. hub and spoke; location and design of distribution centres e.g. use of cross-docking
- Return: an earlier blogpost discusses the process of bringing products back to the organisation at the ‘end of life’, but also for recall and returns that cost money and other ‘re’ actions that could earn money for an organisation
- Circular Economy: discussed in an earlier blogpost; steps taken to create ‘closed-loop’ supply chains that include a high level of the ‘re’ terms. Design products to include end-of-life supply chain actions. Repurpose distribution and maintenance networks to incorporate collection, re-manufacturing and recycling
Resilience: the ability of an organisation’s supply chains to reorganize and continue to deliver its core function (to provide Availability), despite the impact of external and or internal shocks to the system. Resilient Supply Chains contain three phases:
- Readiness is working within a Supply Chain Risk Management scenario as discussed in an earlier blogpost. This includes the identification and possible mitigation of supply chain risks
- Response is a plan of action through a Supply Chain Business Continuity Plan (BCP). This should address at least five factors:
- Make or buy decisions
- Suppliers’ capabilities for critical items
- Alternative suppliers, contract manufacturers and trade lanes
- Inventory policies and demand signals
- Logistics processes including IT capabilities
- Recovery is through a Supply Chain Disaster Recovery Plan, which should address at least four factors:
- Structure and locate (with facilities) a supply chain group employee-based recovery team with centralised decision, co-ordination and liaison responsibilities. Plan working shifts and responsibilities for an extended emergency situation
- Identify and enable replacement communications channels (including secure IT capability) internally and externally through at least the core supply chains
- Identify alternative locations (owned, leased or 3PL) to provide ongoing logistics services
- Enable alternative ordering and payment arrangement for suppliers
To implement Resilient Supply Chain for your organisation will require a change in the corporate understanding concerning the role of supply chains. Being resilient will require a rethink about: relationships in supply chains, the role of redundancy for inventory and facilities and building adaptability and flexibility through the supply chains.
Adaptable and Flexible Operations
The diagram above provides a definition of Adaptable and Flexible as it applies to Supply Chains. To attain this definition requires different approaches, depending of the positioning of operations to satisfy customer demands.
- A responsive focus is on the shortest customer order process cycle. It applies to businesses that Make to Stock, import of finished goods and businesses in the resources sector
- Higher demand variability may require excess capacity in manufacturing and distribution assets that are closer to the customer. Inventory buffers may be required, based on the form and function of inventory at critical nodes in supply chains
- An agile focus is on minimizing the impact of Variability through operations. Upstream in the process is Make to Order (MTO) of a base product with options and Assemble to Order (ATO) is close to the customer. For equipment, use the One Minute Exchange of Dies (OMED) quick change approach. This sequence also applies to process items (called ‘mix and stir’ businesses) utilising small holding tanks and quick changeover of filling units
To achieve adaptability and flexibility, businesses should at least implement the following:
Standard parts and processes: Design engineers and chemists should justify the need for multiple items with similar specifications. Parts should be interchangeable and generic wherever possible, so that items can be moved between owned or contract factories that are similar in design and processes. Note that contract manufacturers prefer stability; for flexibility, provide them with standard parts and processes.
Processes to be concurrent rather than sequential: This reduces delays in the process of accepting and sequencing a customer order, but it requires capable employees that are able to meet critical path deadlines
Postponement: Products and processes to be designed such that decisions concerning each stage in the process can be postponed to await confirmation of required needs
Cross-trained employees: This provides flexibility within the organisation. Employees should be recognised and rewarded for the range of skills obtained, which the business can utilise as required
Manage supplier relationships: Whether there are a few critical tier 1 suppliers or multiple suppliers, manage supplier relationships in a manner that aligns with the Procurement strategy
Climate Change and other disruptions will be a feature of supply chains for the foreseeable future. The steps described in this blogpost will assist supply chain professionals to understand the requirements and to sell the process throughout your organisation.
Thank you for reading the blogposts and other free resources provided by Learn About Logistics through 2020. As it is mid-summer in Australia, Learn About Logistics is taking a break. The next blogpost will be published on Monday January 25. We all hope that 2021 will be a less disruptive year.