Lead Time terminology
Lead Time is an easy concept to understand, but difficult to control when external to your business. Lead Time is the amount of time between the commencement and completion of an operation or process. Transit Time is the time taken for an order to be delivered to its final destination from a designated pick-up point. ‘Order to Ship’ Time identifies the lead time under control of the supplier, from when an order is placed with a supplier until the order leaves their premises. The Cumulative Lead Time for an input item or product is the total time from placing an order to receipt of the goods; that is the sum total of lead times for input materials, factory production and delivery (transit time). The multiple steps in this process increases complexity and the risk of delays.
As an example, the Cumulative Lead Time quoted from a supplier in Shanghai, China to Melbourne, Australia is 56 days, but the Transit Time is 21 days, including the Steaming Time for the ship at sea at about 12 days. These figures can vary due, for example, to weather conditions, the shipping company deciding to slow the ship’s speed or berths and cargo handling equipment not available at the destination port. Even more scope for variability is a cargo from Santos, Brazil to Sydney, Australia, where the transit time for cargo is 52 days, with possible transhipments at Valparaiso, Chile and Auckland, New Zealand. In this case, the Cumulative Lead Time could exceed 90 days, with many opportunities for problems.
The activities between the Cumulative Lead Time and Transit Time is where ‘things go wrong’. Think about order entry, production scheduling, production, dispatch, port activities, pick up and delivery from the port, warehouse acceptance and put away, dispatch to retail store and delivery to the customer.
Lead Time is not a static number and one of the factors is Load. This is the amount of work that has been loaded into a known and available capacity. New orders must wait for available slots of capacity as current capacity is consumed, so lead times can change.
Causes of Lead Time Variability
The change in Lead Time for the same task at parts of a supply chain over repeated occasions indicates Variability in the process. All the variabilities through a supply chain provides Variability of the Cumulative Lead Time, with the main causes being:
Demand Fluctuations: Unplanned increases in order volumes from customers can impact delivery lead times and their variability. They also affect production schedules, where an increase in volumes can overload capacity, which then affects the lead times for material and component schedules. Although input materials and components are ‘dependent’ items, with orders dependent on the volume of finished goods, uncertainty in supply chains can require ‘just in case’ inventory of critical items. Likely changes in customer demand caused by seasonality or promotional activities for products should be identified within the Sales & Operations Planning (S&OP) process.
Supplier Reliability: Delays in customer order fulfilment and increased variability in lead times from suppliers can increase, due to ‘rush’ orders from some customers that exceeds the capacity load. Also scheduling issues caused by inbound material and component shortages and production delays caused by machine problems, product quality issues and labour disputes. There is now a heightened risk of IT security issues and damage at a supplier’s facilities caused by wind, fire and flood.
Transport Delays: Caused by capacity or operational problems at sea and air ports; carrier capacity constraints in ocean, air and land; weather-related disruptions on land and at sea and traffic congestion. Customs authorities can cause delays for international shipments.
The Forrester or Bullwhip Effect is a long studied situation, where orders on suppliers will tend to have a larger variability in lead times than the variability of sales to buyers. This can amplify the demand fluctuations through the upstream links in a supply chain and so worsen the Bullwhip Effect, with more uncertainty and more inventory held ‘just in case’.
However, the length of a quoted lead time is not a problem if that time is adhered to and if orders and ship departures are a regular occurrence. If the inventory is designated as ‘in-transit’, its value becomes part of the buying company’s assets and, operationally the inventory is identified as a ‘floating warehouse’, with a calculated availability date.
Lead Time and decisions
Decisions concerning inventory within a company’s supply chains can be affected by Lead Time variability. The most obvious is the reduction in the ability of your business and its supply chains to respond and adapt as market conditions or customer preferences change. In the short-term, service levels and customer satisfaction are affected by delays in order processing and product deliveries caused by lead time variability issues, potentially resulting in lost sales.
When a supply chain experiences variability in deliveries, a ‘buffer’ against uncertainty must be established, with either: more inventory (to reduce the risk of production disruptions and stockouts), transport capacity (e.g. emergency air freight), or time (customers must wait or there is higher ‘out of stock’ (OOS)). Carrying excessive buffer stocks inflates the cost of holding inventory, increases working capital and reduces profitability.
The variability of delivery lead times can, at the extreme, become the Lead Time Syndrome. The effect of increasing lead times will cause a business to experience a cycle of missed delivery dates, with the potential for unnecessary capital expenditure, as shown in the diagram.
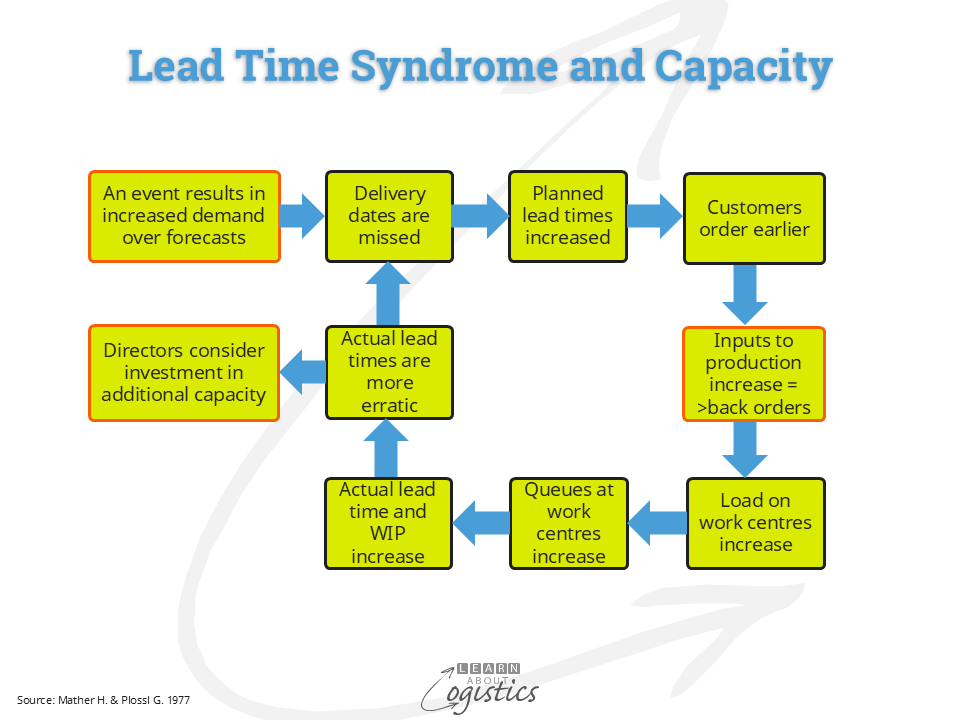
As delivery dates are missed and planners increase the planned lead times, customers are likely to order more items to cover the increased lead time. Back-orders will increase, as erratic ordering behaviour results in even larger variability. A continual increase in lead times and back-orders makes the situation worse.
As has happened, directors of the supplier business may authorise the construction of new facilities. When the new facility commences operations, capacity is increased, therefore the lead time for new orders is reduced. As customers have already placed orders to cover the extended lead time, they have no need to place new orders. The supplier will then progressively reduce the lead time to attract new orders until the lead time falls back to the original level and maybe the new facility is closed.
So, managing outbound lead times in a business is about the management of capacity. But, for inbound materials and components, the Supply Chains group must understand and respond to Lead Time Variability as an important measure for its effect on a range of supply chain decisions.