Supply Chains Network strategy model
Your organisation’s Supply Chains Network strategy is likely to be in place for between three and five years. However, it needs to be reviewed and possibly updated annually to reflect changes in user and supplier markets.
An organisation’s Supply Chains Network strategy should be a consolidation of at least three strategies: Procurement, Operations Planning and Logistics. There could be others, such as customer service and supply chains finance and legal, but that depends on an organisation’s size and structure. To achieve an alignment of the strategies, each should be built within a common framework or model. This is shown in the diagram below.
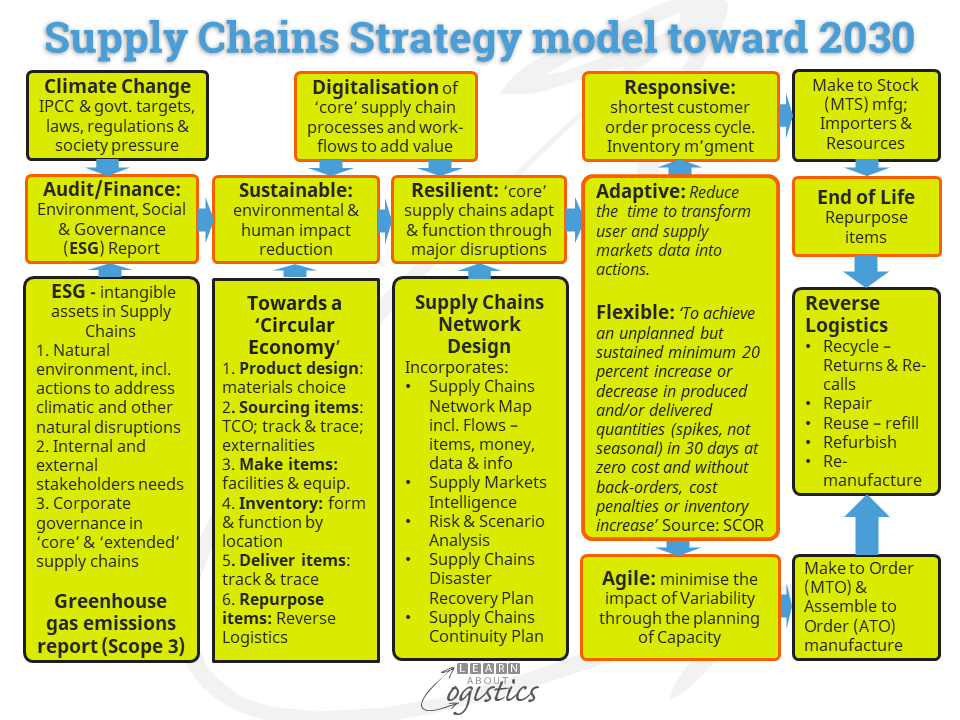
The factors outlined in red are the most likely requirements of your organisation’s Supply Chains Network until the end of this decade. The proposed actions are outlined in black.
Supply Chains are a complex network of risks that interact with each other in ways that are not necessarily known and with emergent (not planned) outcomes. To understand and manage these risks requires that the three functions at the centre of Supply Chains processes should plan their organisation’s supply chains as one group.
View the diagram
From the left side, the increasing output from the Supply Chains group will be the reporting requirements for audit and finance firms. This is the reporting against Environment, Social and Governance (ESG) factors and Greenhouse Gas (GHG) Scope 3 emissions, through the ‘core’ supply chains (i.e. between your organisation and its Tier 1 suppliers and customers). Reporting on your organisation’s ‘extended’ supply chains (out from Tier 1 suppliers and customers) will be an increasing requirement.
The previous blogpost discussed the requirement for Greenhouse Gas emissions Scope 3 reporting. Initially it will affect large companies, but to complete their reports, large companies will require input from their Tier 1 suppliers; in turn, they will require input from their suppliers. To provide the data in a timely manner will require the alignment of systems and processes across ‘core’ supply chains.
The audit/finance reporting requirements will lead to actions that can make your organisation more Sustainable. This requires the Supply Chains group to take an increasing ‘circular economy’ view of planning and execution activities, commencing with the choice of materials in products, as shown across the six factors under ‘circular economy’ in the diagram.
To be Sustainable over the long-term requires your business to be Resilient – at the very least, along the ‘core’ Supply Chains; enabling them to adapt and continue functioning through major disruptions. To achieve a high level of Resilience requires knowledge. This comes from understanding two elements of your organisation’s supply chains:
- The ‘Flows’ of items, money, data and information through the supply chains and
- Supply Markets Intelligence concerning the status of supply markets that influence the organisation’s decisions
This knowledge enables the Supply Chains group to structure a Risk Analysis and to use that information as input to Scenario Analysis. These analyses enable the structuring of the Supply Chains Disaster Recovery and Continuity Plans, for that time when a major disruption overwhelms the organisation.
To be a Resilient business requires the organisation to be both Adaptive and Flexible; how these are achieved will differ between organisations.
- Adaptive requires the quick response to events. This means the elimination of time delays in transforming user and supply markets data into actions. It includes eliminating delays in order processing, such as sign-off by technical and finance functions of customer orders. Reductions in process time enables a business to have a more Responsive focus to customers’ needs
- Flexible is defined in the diagram using the SCOR definition, because this is concise and can be measured
As part of being Responsive, Operations Planning uses inventory and capacity as the two ‘buffers’ to smooth fluctuations in demand and supply and so respond to customer orders in a timely manner. In the Make to Stock (MTS) sectors (which include manufacturers, importers and resources businesses), the past three decades (at least) have seen manufacturing outsourced, or if maintained, the production assets have been more highly utilized. In both situations, the ability to use capacity as a buffer against Variability is not available. The outcome is that in MTS planning, inventory is the buffer to absorb demand and supply Variability.
For businesses that satisfy customer demands through Make to Order (MTO and Assemble to Order (ATO) processes, the Operations Planning objective is to minimise Variability through managing Capacity. This is to have an Agile focus.
The Scope 3 emissions reporting requirements include ‘end of life’ repurposing of an organisation’s end products. The diagram identifies the five processes used to re-purpose an item. Common to them is the planning and use of Reverse Logistics.
The final element in developing the Supply Chains Network strategy is Digitalisation. This is the identification and implementation of digital technologies that support Sustainable and Resilient ‘core’ supply chains processes and workflows that add value.
Generally, it is easier to justify and implement operational hardware, such as Industrial Internet of Things (IIoT), vehicle sensors and warehouse robotics, because the project is confined within Logistics facilities and only requires co-ordination with IT. On the other hand, software, in the form of applications, analytics and markets intelligence is more difficult to justify and implement.
In many organisations, the terms Supply Chain and Logistics are not clearly understood. Also, not understood is that the three supply chain functions operate within Flows, both outside and through the business as a ‘complex, non-linear, adaptive system. The process can therefore be hampered by the lack of a clear description of why the software is required, the outcomes expected and an implementation plan that is accepted by all involved parties.
The future model
This model provides a basis for selling to senior management the proposition that supply chains are a ‘value adding’ part of the business. Learn About Logistics expects similar models to be in use until the end of the decade. Then, a new Supply Chains Network strategy model is likely to be developed. This could be based on growth of the ‘platform economy’; an emphasis on regional/local markets and manufacturing; technologies such as 3D printing maturing and gaining acceptance and financial markets becoming more decentralized.