Supply Chains process gaps
There are occasional articles that discuss misalignment or gaps in organisations’ supply chains, which occur in processes, information flows, and IT applications. Examples of the gaps are:
- Supply Chains group collaboration does not exist (at the minimum between Procurement, Operations Planning and Logistics). Each function reports to different executives e.g. Procurement reports to Finance, Operations Planning to Manufacturing or Operations and Logistics is lost somewhere in Distribution
- Transport planning within the Transport Management System (TMS) does not interface with distribution planning in Distribution Requirements Planning (DRP)
- Demand Planning (within Sales) does not interface with Revenue Management (within Finance) or with Operations Planning
- Planned Orders for manufacturing in Materials Requirements Planning (MRP) does not interface with the Procurement Sourcing & Supply Markets Plans
- The output from Sales & Operations Planning (S&OP) does not interface with the Sales & Operations Execution (S&OE) process
These gaps should be identified as supply chain risks for an organisation, because they require attention. An important gap that can be investigated for improvement is the last on the list – a Planning and Execution gap.
Planning and Execution gap
The challenge appears to be that Tactical Planning requires data structured in the aggregate, while Operational Scheduling requires details for each Stock Keeping Unit (SKU). So, how to reconcile this challenge and enable data to be translated between the two levels? The approach is to use the Bill of Materials function that resides in your organisation’s ERP system. The diagram below illustrates the approach.
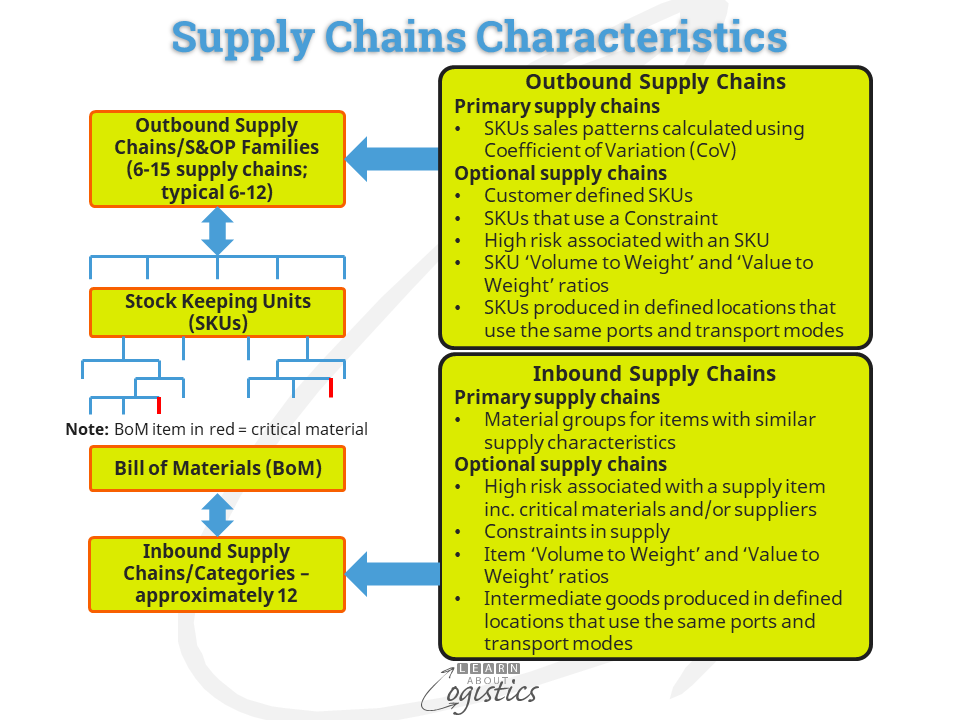
For the S&OP process, SKUs are grouped into ‘families’, which are also the outbound supply chains for the business. A software module that aggregates SKUs into families/supply chains would be of assistance. The criteria for establishing the Outbound Supply Chains is shown on the right side of the diagram, with an explanation below:
Primary outbound supply chains
- Sales analysis using CoV identifies the supply chains and each supply chain requires a different approach to serving customers. The use of CoV in planning outbound supply chains was discussed in a previous blogpost.
Optional outbound supply chains to allow for specific characteristics:
- Customers with specific requirements concerning their defined SKUs; for example, vehicle assemblers, pharmaceutical companies and supermarket chains
- SKUs that utilise a Constraint in the business, which restricts output and therefore potential sales. A Constraint can include specific equipment or access to materials, either obtained on a seasonal basis or deemed to be a ‘critical’ supply item
- Risks associated with the SKU: contamination; perishable; ageing (use by date); flammable/explosive; and theft
- ‘Volume to Weight’ and ‘Value to Weight’ ratios of SKUs, as these can influence the selection of transport modes
- SKUs produced/contract assembled for the enterprise in defined countries and locations and using the same modes of transport. These SKUs can be consolidated within containers to reduce transport costs
Each SKU has its Bill of Materials (BoM), which defines the materials and intermediate goods used in constructing the SKU. There should be a facility for customising data fields in the BoM. This enables specific features to be identified (such as a critical material) and linked to a supply chain for use in S&OP. Also, a capability to translate the SKU measurement (weight, volume, packaging etc.) into the standard unit of measure used for S&OP (tonnes, litres, standard shipper etc.).
Although the output from S&OP is aggregated by period using a standard unit of measure, its use of the BoM structure means that the gross numbers can be disaggregated back to individual SKUs, based on historical sales percentages. This means that the Plan from S&OP can be entered into the S&OE Master Schedule as a forecast for the applicable future periods.
The BoM requires the ‘quantity per’ for each supplied material and intermediate good, so the S&OE Master Schedule S&OP forecast material requirements can be calculated for input to the Procurement Category Management process. As shown in the diagram, the Categories and sub Categories of supply are the Inbound Supply Chains, based on the material item’s characteristics that influence supply.
Primary inbound supply chains
- Material group for each supply item e.g. metals, ingredients, electronic assemblies, packaging etc. because each item in a group is likely to have similar supply characteristics:
- Each Materials group is divided into Categories and where required, sub-Categories. For example, a food company has the ‘Ingredients’ group. This may contain a Category named Sweeteners, which has a sub-Category named Glucose
Optional inbound supply chains
- Risks associated with a supply item: contamination; perishable; ageing (use by date); flammable/explosive, and theft. Also, critical materials and/or critical suppliers (e.g. monopoly or duopoly) that have high risks associated with supply. A facility is required to enable ‘risk’ supply items in each Bill of Materials (BOM), to ‘roll-up’ into their S&OP supply chain (or ‘family’) for evaluation through the S&OP process
- Constraints in supply, such as a port that operates at capacity (with delays) or seasonal capacity constraints for a material
- ‘Volume to Weight’ and ‘Value to Weight’ ratios of supply items that may influence the selection of transport modes
- Intermediate goods produced by suppliers or contractors in defined countries and locations and using the same transport modes at Links in a supply chain
Use Available to Promise capability
Your organisation requires a software application that provides customers and internal functions with ‘one source of truth’ regarding Availability of, and the capability to deliver, products. This is called ‘Available to Promise’ (ATP), which can be used by senior management, Customer Service, Sales and Operations Planning. With the Outbound and Inbound supply chains defined and linked, using the BoM facility, there is data available within your organisation’s ERP system or as a stand alone application, but with interfaces (APIs) to internal applications.
The diagram below identifies the main elements required for an ATP. Similar to the software applications for S&OP, the requirements for ATP are data and information gathering and presentation, rather than complex analysis.
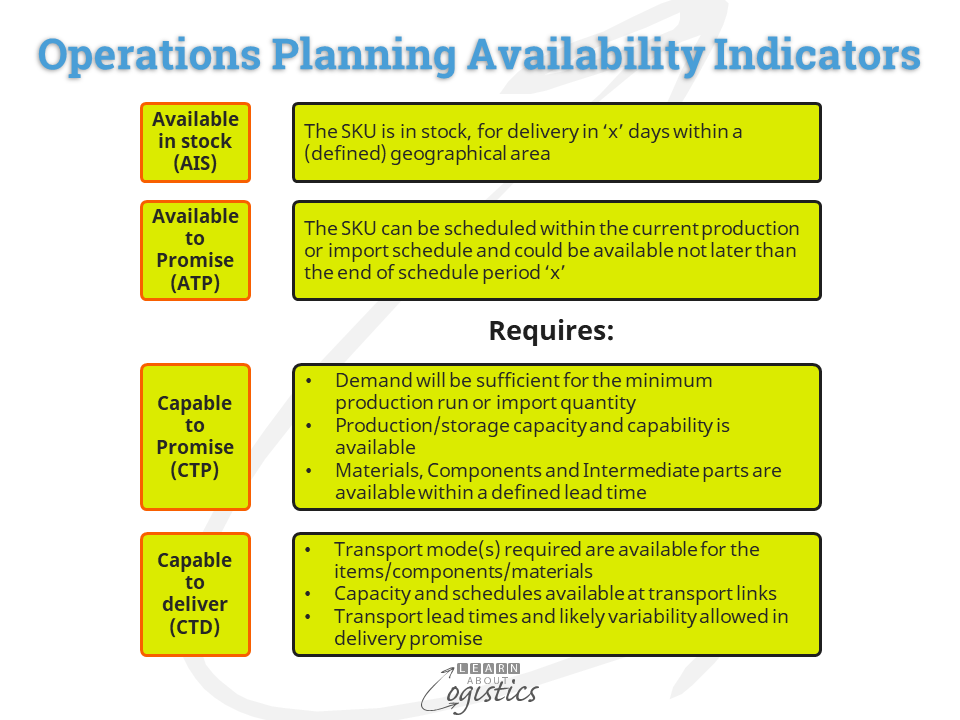
In articles about supply chains, terms like agility, responsiveness and flexibility are commonly used expressions, but often without definition and explanation. Instead, it is better for improved outcomes to identify, in simple terms, the principles concerning outcomes and the steps to achievement, as outlined in this blogpost.