Inventory is an asset
Logistics is the science and art of providing availability of items for users. Inventory is all the items purchased and/or made by a business but not yet sold. A core part of the logistician’s role (in a brand company or at a 3PL) is to optimise the amount of inventory within a shipper (or brand owner) organisation.
Inventory appears in company accounts as an asset, but commencing in the 1980s with the Just in Time (JIT) movement, inventory was viewed within operations as a cost to be eliminated. Accountants have only ever known inventory as a cost; the budget for inventory allowed in a business is preferably a ratio to sales or cost of goods sold (COGS).
However, with an increase of disruptions in supply chains through 2020, more businesses are reconsidering their attitude towards inventory. There is now a role for Logisticians to work with finance and accounting professionals to agree on the reasons for this change.
The required outcome is to change the budget driver for inventory from a ratio to a calculated and justified figure, based on the current known structure and variables of your organisation’s Supply Network.
The value of Inventory to your business
There are three main business reasons for holding inventory:
- To provide a buffer between demand and supply for an item.
In earlier times, brand companies had two potential buffers in their supply chains. One was capacity in manufacturing and distribution; the other was inventory.
However, using capacity as a buffer has been effectively lost. This is due to past cost reduction drives, which provided higher utilisation of machines and other assets (therefore no spare capacity); also the outsourcing of manufacturing removed capacity. This leaves inventory to be the buffer against variability of demands from customers, consumers or internal sources and the supply of items through an organisation’s Supply Network.
2. Inventory used as part of business strategy:
a. Anticipation inventory: Inventory is built in advance of a demand. It can be for:
- postponement inventory in an Assemble to Order business,
- seasonal high demand,
- for public and religious holidays,
- to overcome potential shortages caused by the planned shutting of a factory for maintenance, extended holiday periods or supplies of a purchased material to be restricted
b. Hedging inventory. Companies that purchase traded commodities, such as natural fibres, grains and metals buy additional physical materials when the global price is considered to be low (although this may not be a correct assumption).
However, instead of investing in physical goods, the company can ‘lock in’ the future price of the material through trading contracts for future purchases on the international commodity exchanges e.g. London Metals Exchange (LME) and Chicago Board of Trade.
c. In-transit inventory. The availability of global supply can result in increased distances travelled for materials, parts, components, intermediate or semi-finished goods and finished products. This can be between suppliers and the brand owner’s facilities, or their outsourced manufacturers, original design manufacturers (ODM), logistics service providers (LSP) and agents. If the items are purchased ‘ex-factory’ by the brand owner and they arrange transport, the inventory value becomes part of the company’s assets and therefore is designated as in-transit inventory (a ‘floating warehouse’).
3. To meet the in-full and on-time expectation of customers:
a. Cycle inventory. Inventory to be held for an SKU at the mid-point through the replenishment cycle (half the order quantity), based on the most appropriate order policy. The replenishment cycle can increase due to shipping time and delays and delays in providing intermediate items from contract manufacturers, due to complexity of design and components or materials required from multiple countries.
b. Fluctuation inventory. Inventory held in excess of the cycle inventory to overcome uncertainty associated with unplanned events. This calculated inventory is called either safety stock, reserve stock or buffer stock and accepts that ‘on average’, 50 percent of the time the demand for finished goods is below the forecast, therefore safety stock is not required.
Holding a calculated ‘safety stock’ allows an organisation to reduce its total operational costs, due to fewer disruptions. However, there is a cost incurred from holding inventory. The total cost of an item includes the material costs, the manufacturing costs, the costs incurred in buying and transporting the SKU and the costs in holding an item at a store or warehouse. While the costs can vary, an easy to remember approximate holding cost is 24 percent per year or 2 percent per month for just sitting there!
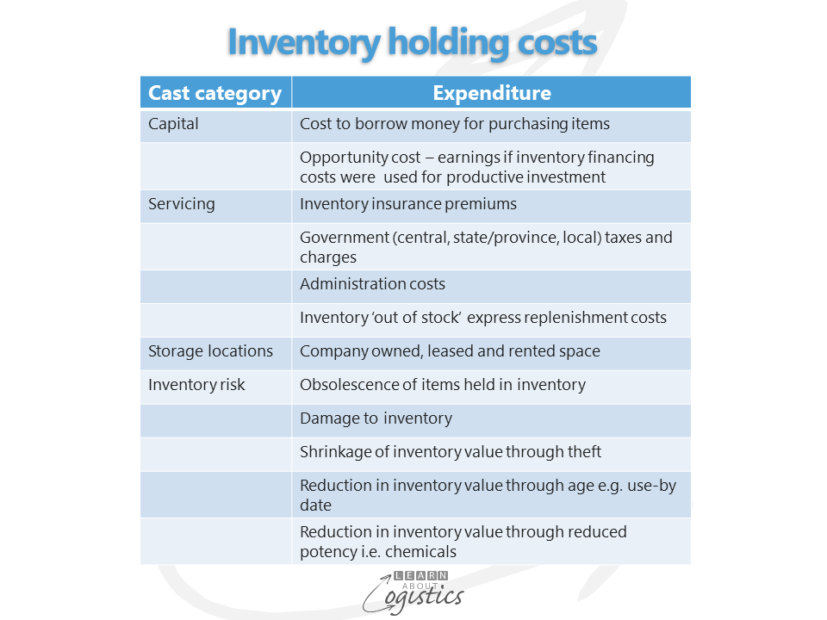
A Supply Network is complex
The process for a product is Plan, Source, Make, Deliver and Return. However, to enable this process requires a Supply Network, which is a complex of nodes and links that no person fully understands or controls. It is a Complex Adaptive System (CAS).
As discussed in a previous blogpost concerning a CAS, the outcome from events and any subsequent actions at nodes and links in a supply chain are both Emergent and Cumulative and cannot be predicted with any certainty.
Therefore, a brand company must effectively manage its external business relationships and its own operations through recognising and mitigating the supply chain risks within Procurement and Logistics. Within Logistics there are Inventory Risks
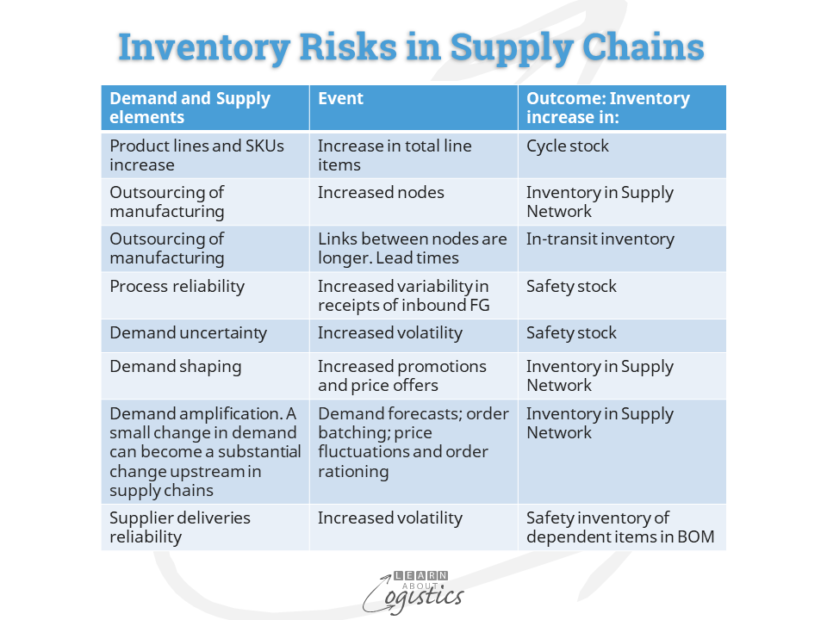
To better understand the Inventory Risks, Logisticians need to develop a Supply Network Map; as one of the inputs, identify the ‘What and Where’ of Inventory by either product group or SKU:
- In what form are inventories required e.g., raw materials, intermediate or semi-finished goods, work in progress (WIP), finished goods and
- For what function e.g., cycle stock, safety stock, in-transit inventory, anticipation, hedging, postponement, pre-build inventory to support market launches, support a ‘sales package’ of high and low selling SKUs; slow and obsolete (SLOB) inventory etc.
- Where should the various inventories be held – the Location i.e. supplier premises; at a 3PL; in transit; owned and leased premises, customer location, supplier distribution centre, 3PL for intermediate items, etc.
The approach of considering inventory from a business aspect can help to ‘win-over’ accountants. Identifying the business value of inventory, Inventory Risks and the ‘What and Where’ details provides a Logistician with the initial facts to argue the case with the Finance and Accounting group for inventory to be recognised as a corporate asset rather than a cost.