S&OP is a process
The complexity associated with flows through supply chains means that to simplify processes can only help to achieve objectives. And that includes the use of software. There are any number of software suppliers willing to sell applications and tools, but are they necessary and do they complicate the process?
The Planning process is Sales & Operations Planning (S&OP). It is important for all involved in the supply chains of a business to recognise that S&OP is a process, not an IT application. An old saying is that we should “learn to walk before we run”. And because very few businesses that need a planning process have implemented a correct S&OP, the majority need to “learn to walk…”.
This means to ignore articles and presentations which propose that you, for example “…integrate the entire ‘end-to-end’ supply chains so they can run most processes and decisions through real-time, autonomous planning.” This type of advice is a recipe for disaster, similar to those experienced with too many implementations of ERP systems, which promised a world of savings and instead cost plenty, because the basics were not understood.
It is important to be clear about the meaning of Planning thinking into the future regarding the activities required to achieve a desired goal. The key word is thinking. Planning is not about actions or doing – that is the role of Scheduling. An article noted that “Planning must be a process more concerned with policy and objectives than analysing large volumes of data”.
The S&OP process
The Aim of each meeting through the S&OP process is to review the future intentions (i.e. past the ‘freeze’ period) of Sales and Operations and their financial feasibility, as shown in the diagram.
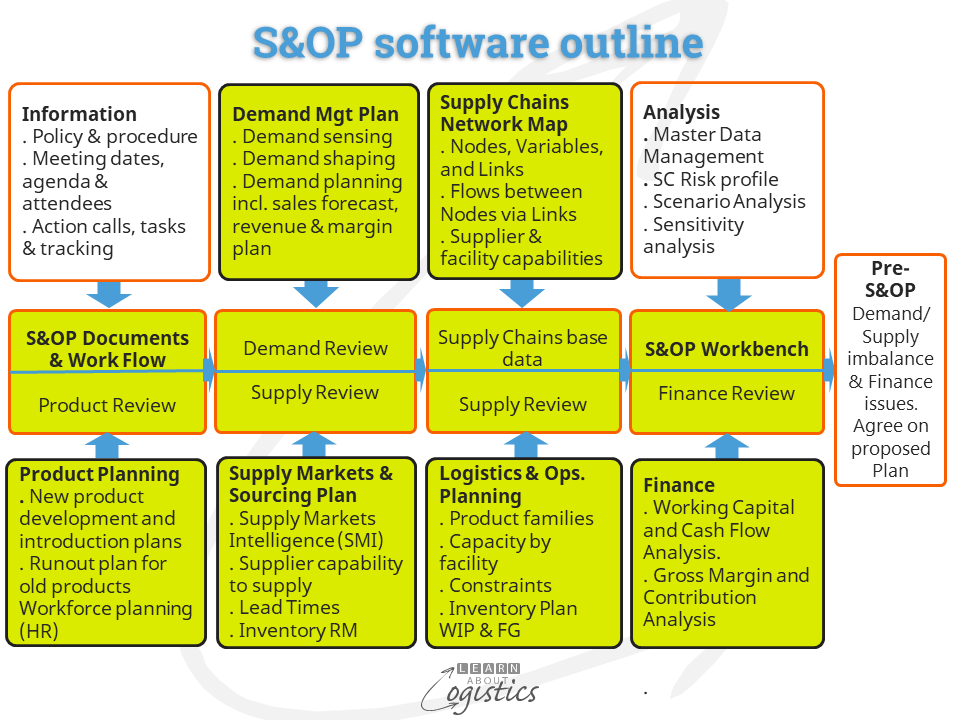
The diagram illustrates that data and information inputs to the process (shown in colour) are mainly held in application external to the S&OP process. Due to circumstances within a business, the volume and quality of the information supplied by each function will most likely grade from manual through spreadsheets, to batch update applications (such as the ERP system) and ‘real time, on-line’ applications (which maybe held in the ‘Cloud’). This could be supplemented by email communications and slides.
While these tools limit the development of multiple scenarios, or answering ‘what-if’ questions, or provide a collaborative workflow and exception messaging, accept these initial limitations. Getting the S&OP process working and enabling a collaborative culture to develop is more important, and indications of success with the S&OP process will hasten approvals for software upgrades. While not the most desired situation, a lack of the ‘right’ computer application(s) is not an acceptable excuse for delaying the implementation of S&OP.
S&OP software needs
The diagram provides examples of the inputs required. As noted, the coloured areas are external inputs, while the non-coloured areas identify the initial S&OP needs:
Information: Documents and Workflow to Facilitate meetings
The administrative aspects of the S&OP process that facilitates the connection of people and information:
- S&OP policy and procedures
- Meeting dates over the forward six to twelve months
- Agenda and attendees for each type of review meeting in a S&OP cycle
- Identify ‘product families’ used in the S&OP process and standard unit of measure
- Action calls: identify attendees’ ‘to-do’ tasks from the S&OP Executive meetings and tracking of progress
- Access to documents. Enable sharing of S&OP information and data between participants
- Questions and responses posted to and from participants
Analysis: S&OP Workbench
This provides analysis concerning the impact of alternatives, to enable improved decisions at the Pre-S&OP and S&OP Executive meetings:
- Master Data Management: consolidates date from multiple sources and by multiple time buckets (month, quarter, annual). It requires evaluation of customer and item masters, including names, addresses date format units of measure, time horizons, bill of materials (BOM) structure etc. Also, the levels of accuracy required (gross margins, inventories, capacities, service levels etc.), as items are rolled-up from product line level to their S&OP ‘family’. Identify alerts and exceptions in the data
- Scenario Analysis: Create different scenarios e.g. pessimistic, optimistic and most likely impact on the future state of the organisation’s supply chains. This analysis is based on assumptions and projections from the Review meetings. Due to it being a Planning environment, the output is not required to be ‘on-line and instantaneous’.
- Simulations: run multiple scenarios to predict how a system or process will perform under different conditions and the impact of risks and opportunities. This provides for Predictive Analysis
- ‘What-if’ (sensitivity) Analysis: to identify the most influential variable in a model or scenario
- S&OP Plan: over the planning horizon to achieve a Demand – Supply balance
Pre-S&OP review meeting:
The pre-executive S&OP meeting is for the direct reports to the executive team members who resolve issues from each of the review meetings. It is also where Finance provides inputs, concerning revenue, margins and cash flow, based on that period’s review meetings. This meeting allows the S&OP plan, trade-offs and issues to be packaged for the S&OP Executive meeting.
The software requirements are to enable visual packaging (wherever possible for ease of understanding) of the proposals to be presented at the Executive S&OP meeting.
Collaboration is the Aim of S&OP
The word Collaboration comes from the Latin, meaning to work (or labour) with, and the Aim is to achieve a goal. Prior to Collaboration it requires Co-operation (a willingness to work together across functions) and Co-ordination (to use a common terminology and processes; to share data and information).
The implementation journey begins with improvements to co-operation and co-ordination between functions, which should start to appear about six months into the implementation. But to achieve full collaboration to become the ‘way we operate’, may take up to three years.
The time for S&OP participants to feel comfortable with the process and the beginnings of collaboration provides sufficient time to identify the data and information input requirements. The challenge is that in these days of ‘instant’ improvement, are you and your colleagues willing to work for this length of time at improving the process and results?