Complex and Complexity
When discussing the topic of Supply Chains, the terms Complex and Complexity can be regularly used. But, while sounding similar, they are different. Complex is used when describing Supply Chains Networks. These are difficult to understand, because relationships between parties in the Network can be dependent, independent or interdependent, with different responses that depend on influences from within the system or from the external environment. Complexity is used when discussing the Supply Chains operations of a business; these can be improved with a predictable outcome.
The table below provides a view of Complexity in a Core Supply Chain. Additional explanation then follows.
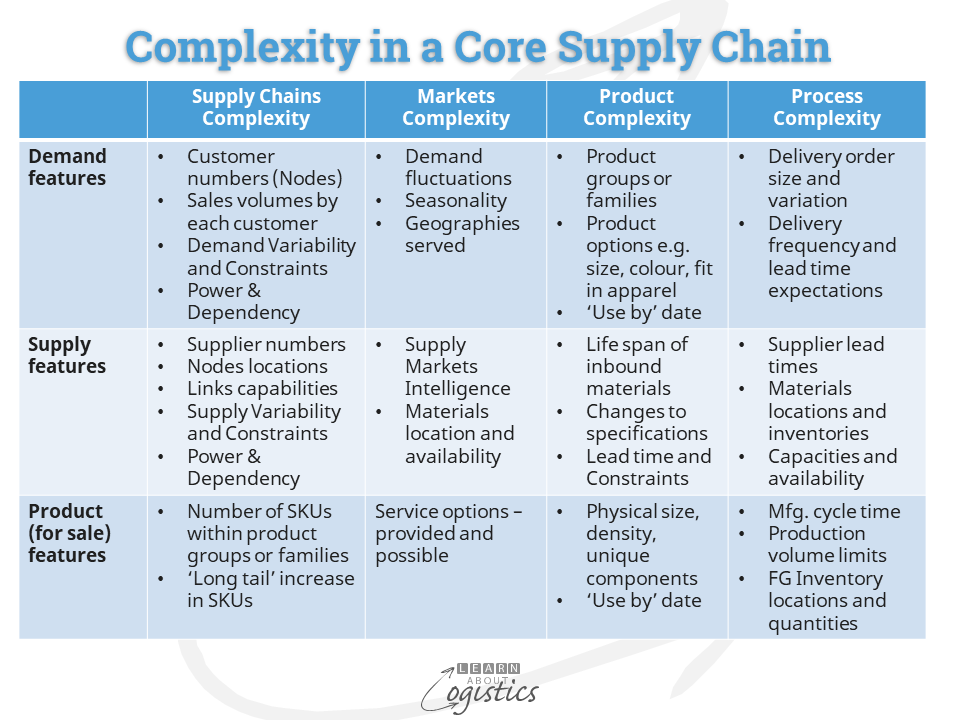
Complexity in your Core Supply Chains
Customers
Each customer has different requirements concerning their frequency of orders, size of an order, delivery requirements, level of customer service expected, payment terms etc. The more product customisation and service options that are offered by Marketing only increases the opportunity for customers to accept them, especially if they are priced incorrectly. To reduce this Complexity requires Logistics to establish the ‘Cost to Serve’ for each customer and for Sales to then manage the customer’s expectations concerning value received and the price they are prepared to accept.
Information
Actual demand and supply visibility can be obscured through the way that data and information is filtered and modified within a business and as it passes from one organisation to another. Demand Amplification distorts demand signals – a small change in demand at a point in a supply chain can cause a substantial change in upstream demands. This action means that data used as input to Operations Planning at each Tier of supply is incorrect, forecast accuracy is reduced and more costs are incurred. The main causes of Demand Amplification are:
- Demand forecasts: using only internal order and shipment data
- Order batching: to meet efficiency targets
- Price fluctuation: involves ‘deals’, such as volume buys or ‘investment’ buying, where a lower unit price is offered for higher purchase quantities
- Rationing and shortages caused by large buying orders: Planners may increase lead times rather than manage capacity
Product
Occurs when there is a high number of materials, components or sub-assemblies. This can be associated with the lack of item commonality across the Bills of Material, which can affect flexibility in scheduling to vary the product mix or volumes in production.
Laboratory or design office decisions are made concerning the choice of materials, components and packaging. These may influence Procurement decisions concerning sourcing in supply markets, which can affect the total cost of ownership (TCO) for items and therefore the cost of the product.
Product Range
The range of products and/or services offered to a market is more likely to increase rather than decrease. It is usually easier for Marketing to introduce new products or services; additional line (or brand) extensions and pack sizes than it is for existing products or services to be discontinued. This situation extends the ‘long tail’ of products with low sales.
If a business does not have an ‘agile’ production structure that responds to low volume production orders, the outcome is a reduction in forecast accuracy and discounted sales of excess inventory. The biggest threat is that under standard costing, the low volume products will not be charged sufficient overheads to cover their complexity, while high volume products will carry a dis-proportionate share of overheads that reduce margins and influence Supply Chains and Marketing decisions.
Planning
To achieve the Availability objective of the supply chains group requires managing three factors – capacity, inventory and lead times; the building blocks for managing the flow of items.
Managers may say they know their capacity and its utilisation; but which capacity measure is being used – rated, productive, demonstrated, budgeted or other? And how is capacity affected by uncertainty in demand for the company’s finished goods? Is it dependent on the capital intensity of the business, the lead time to change (or flex) operations and the cost?
Inventory not only costs money to buy, process and store but, to meet the business objectives it must be in the:
- right location (customer, company or 3PL warehouse, suppliers)
- most efficient form (RM, semi-finished (postponement), FG) and
- most effective function (cycle, safety, seasonal build etc.)
- trade-off with capacity and lead times that are affected by inventory decisions
Bringing responsibility for capacity, inventory and lead times into one group is the first step in changing an organisation from silo thinking to thinking about flows – of item, money, data and information
Suppliers
The number of Tier 1 suppliers dictates the time available for Procurement professionals to build business relationships that contribute to supplier involvement in process improvement, reduced ’emergencies’ and lower transaction costs. Too many suppliers reduces communications and increases complexity.
Achieving the correct balance of Tier 1 suppliers against availability of items requires Procurement professions to work within a ‘supply markets and sourcing’ and ‘category management’ structure so they understand their supply markets and manage the purchased items.
Processes
Within the Core Supply Chains of a business are internal processes and those managed by external Tier 1 suppliers and customers. These processes may have been introduced then modified to reflect requirements at different occasions, naturally building complexity.
While the TLS approach (theory of constraints, lean and 6 sigma) for improving processes is valued, managers in supply chains can drive improvement in processes through MBWA (management by walking around). This requires leaving the computer and discussing with their staff how and why they do things within their job. An added part is the ‘waste walk’ where a manager travels from the end of a process to the start, asking ‘why’ at each step, mapping the formal and informal relationships between elements.
Addressing Complexity
Supply Chains will always incur Complexity. The challenge for Supply Chain professionals is to understand the Complexity that is likely to exist that enables your organisation to be competitive and that customers value and are prepared to pay the asking price.
Because Complexity is an element of Uncertainty, your organisation could potentially create a structure that more easily allows adaptation to changes in the economic and business environment, which emphases flexibility and the capability for re-configuration.