Internal and external collaboration
Collaboration is a term often used in articles that discuss Agility and flexibility in supply chains, requiring digital tools that enable data and information to be exchanged between contracting parties. In addition, the current pandemic has resulted in government requirements for people to work at a distance from others. This has accelerated a trend for employees to work fully or partially from home or a local office.
These two situations appear to be both compatible and technically feasible. If employees are collaborating, then it is an easy step to collaborate with suppliers and customers. Unfortunately this conclusion assumes it is all about technology, but that is incorrect.
Internal collaboration can occur (although not necessarily with success) because it is mandated by management, people are part of a ‘team’, the network is (hopefully) closed and the data and information used and discussed is secure.
When you step outside the organisation, relationships are different, so the emphasis in external communications will differ. However, in both situations the journey to true collaboration requires four steps, which contain more than an IT communication application.
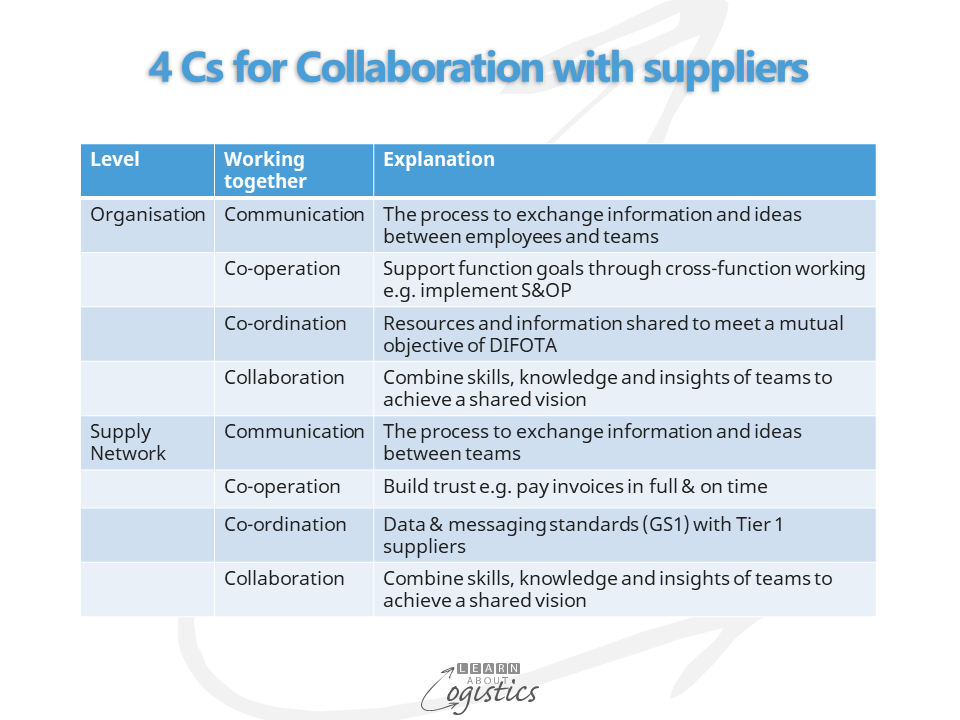
Within a Supply Network, the diagram notes that Co-operation requires building trust with suppliers. In addition to ‘in-full and on-time’ payment of invoices, other initiatives (for buyers with a power advantage) to:
- change the purchasing penalty regime into an improvement regime
- enable access to accurate inventory records that reflects the actual situation
- improve accuracy of sales forecasts, but preferably provide requirements generated from the Sales and Operations Planning (S&OP) process
Collaboration should only occur between consenting adults! Do not ‘collaborate’ if your organisation thinks it rules the supply chains and has an approach in commercial negotiations of “you take the risks and I take the rewards”.
Collaboration, risk and culture
Collaboration can be with customers and suppliers, but in this blogpost, the emphasis is on collaboration with suppliers. Although technology can enable wide collaboration, should your organisation be collaborative with all suppliers? The answer is no, because there are finite resources to build relationship with suppliers (usually in Procurement), therefore your focus should be on the few suppliers that can justify the additional effort.
The starting point is to place all suppliers into a risk-spend quadrant. The suppliers that potentially qualify for collaboration are located in the top left and right quadrants – those with a potentially high risk to the ongoing business.
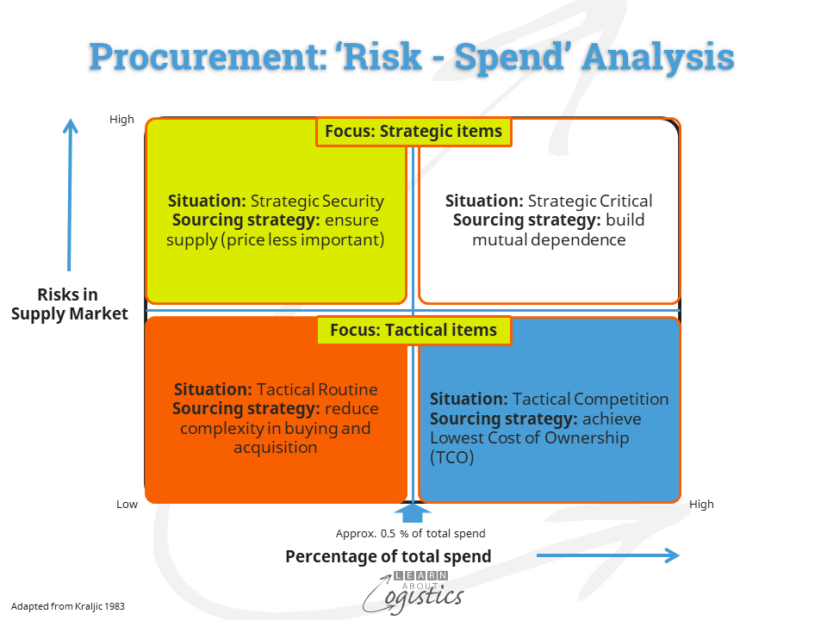
However, this approach only considers the potential for collaboration from a quantitative perspective. The next step is concerned with corporate culture and the supply chain sub-culture of both your organisation and the selected supplier.
A collaborative culture in supply chains stems from a belief by senior management about implementing differing relationships with suppliers, using the risk-spend analysis as the base. A collaborative culture also includes:
- a ‘flow (rather than functional) approach to supply chains
- a ‘team’ approach to working across supply chain functions, with recognition of participation and
- an acknowledgement and measurement of risk in supply chains
Both buyer and seller organisations must hold similar values and feel comfortable in collaborating with other organisations. These are not ‘partnerships’ (the sharing of risk and reward), instead they should be considered as ‘alliances’ between compatible organisations.
However, these strategic relationships can incur conflict if not closely managed; this is why additional resources must be allocated to the relationship. To build an alliance, focus on:
- Develop a shared vision for the alliance
- Understand the challenges associated with the other party’s markets and supply chains and how they could influence the alliance
- Understand the other party’s corporate culture and supply chain sub-culture, through joint project teams and cross placement of employees
- Recognise that each party’s corporate objectives will differ
- Identify and develop common objectives which enhance the benefits of the relationship and are compatible with each party’s corporate objectives
- Decentralize decision making, using a collaboration application. This is a communications and decision making channel which can remotely support both parties. Use it as a central repository of information concerning the alliance
Collaboration applications
Collaboration applications are intended to unify all work interactions within a single online tool, but not all collaboration apps have the same functionality. For supply chains, with multiple internal functions, suppliers, contractors and 3PLs which could be located globally, the ideal requirements are extensive, but necessary, to be of value to the various parties. The list of requirements obtained from various articles could be:
Structure and Integration
- Client portal that provides access to shared files with appropriate levels of permission, for uploading and sharing communications, updates and files
- Integration with applications and other tools via APIs
- Structured workflow to help identify complex task dependencies
- Interrogate the knowledge base and identify issues
Project tasks
- Shared virtual whiteboards with interactive idea mapping tools
- Task status updates and progress visualization charts with ‘to-do’ lists
- Assignment of tasks, with task priority and team members identified
- Calendar and notification system for tracking timelines, updates and deadlines
- Tools such as ‘Kanban board’ (visualize work, limit work-in-progress and maximize flow (or efficiency) and ‘Scrum board’ (visually display current project work that has been taken into the current ‘sprint period’)
- Gantt chart for events and project milestones, showing tasks, sub-tasks, start and end dates, dependencies and assigned resources
- Acceptance testing for new or modified supply chain processes
- Enable the legal sign offs for documents
Communications
- Team collaboration facility that enables team members to access current supply chain data and information, while working from home or travelling
- Voice calls with recording facilities
- Video conferencing, including the sharing of schematics (drawing and diagrams) and co-created documents
- Record live videos, with real-time synchronous editing
Managing collaborative relationships with suppliers is not applicable for all organisations. If your business does not meet the collaboration requirements discussed, then do not try. At the same time, do not talk about ‘partnership’ and ‘collaboration’ just because they are buzz words currently in use.