A new report
A whitepaper was recently published by the Global Supply Chain Institute at the University of Tennessee concerning relations between management and staff in supply chains. While this whitepaper was written for American readers, it contains some useful ideas for supply chain professionals.
The whitepaper is based on interviews with 19 ‘benchmark’ companies. This is a low number of respondents on which to establish definite directions for all businesses with supply chains. As with any published paper, critically analyse the contents before applying them to your organisation.
Analysing a report
In general, beware of ‘buzzwords’ when used in reference to supply chains. A term close to being a buzzword is ‘end to end’ supply chains; but what does it mean? The whitepaper describes it as being between the supplier’s supplier (that is tier 2 suppliers) and the consumer’s shelf (which could mean the customer’s customer – the consumer). This description ignores supply chains for non-consumer items.
However, many organisations do not have the capability to understand the workings of their tier 2 suppliers and customers. The ‘end to end’ term is therefore more often used to define cross-function flows within an organisation, with little or no reference to customers and suppliers, or their respective markets. At the other extreme, the term can be used to describe the flow of items from the ‘mine and farm to the end user’; this could encompass many tiers of suppliers and customers. So, always define the terms being used.
Not a buzzword, but a term which can have different definitions is ‘Supply Chain Organisation’. The whitepaper considers it to be all parts of an organisation that are involved in the movement, conversion and storage of materials and items. This includes (but not limited to) manufacturing, engineering, quality, safety and environmental.
However, this is but one opinion. Another is that the aim of Supply Chains is to provide Availability of items for customers and consumers. To transform materials and components into items for sale requires very different technical disciplines, from those associated with movement and storage of items.
And then there are opinions about the structure of a supply chain organisation. Should it be a centralised group reporting to the CEO? Or a decentralised group of separate functions that co-operate and co-ordinate the ‘flow’ of materials and items? Or something else. The whitepaper does not discuss this topic, but whichever structure is selected will result in different organisation dynamics.
Even before this step, what does the term supply chains mean in your organisation? There are many definitions; from Learn About Logistics it is: ‘the effective flows of items, money, transactions and information through the ‘activity nodes’ and ‘movement links’ at and between supplier and customer enterprises and within the core organisation, for the supply of items that provide value for end users at the lowest total cost’. When all supply chains are considered, they become your organisation’s Supply Network (which may be called the Value Network).
Learn About Logistics identifies two parts in each supply chain. The diagram illustrates the Core – the Extended supply chains are outside of that. As noted above, for most organisations, only the core supply chains are of interest. This maybe the intent of your organisation, but make sure.
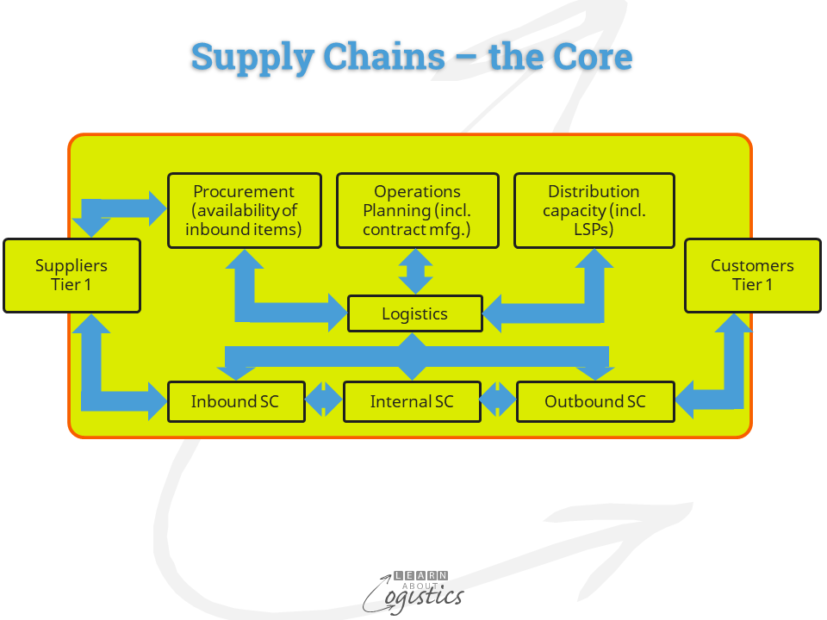
Different opinions concerning the definition of terms used in supply chains are valid under defined circumstances. But your organisation must be clear about the ‘why’ and ‘how’ of the selected approach. What functions, elements, processes and structures become the supply chain group in your business? Whatever definitions are used, make sure that all affected parties agree and use the same definition.
The logistics organisation
The whitepaper considers two drivers of workplace management changes in logistics – retirement of the ‘baby boomer’ generation and introduction of ‘new’ technologies. While applicable in some developed counties, this opinion may not apply for all logistics operations of a business.
The whitepaper does not consider other underlying factors that influence the business of distribution. For example, being viewed as a commodity activity, short contract periods for service providers and low profit margins for logistics service providers (LSPs).
In a number of countries, one response in distribution activities has been to use contract, part time and casual labour. The hiring arrangement is either through direct engagement, a negotiated contract with a labour hire company, or outsourcing the entire distribution function to one or more 3PLs.
If labour hire contracts or outsourcing approaches are adopted, there ceases to be a long term relationship with individual ‘blue collar’ workers. Management relationships will then be with professional, technical and clerical level staff (more likely employed full time), which has a different organisation dynamic. In the whitepaper, discussion of this element concerning supply chain organisations was not considered.
When discussing employment, the whitepaper implies that if there is an ‘open, team based’ approach for a business, then supply chain roles can also be more fluid in their daily activities.
To support this approach, the whitepaper notes the topic of standardisation in supply chains, stating that “newer generations are sceptical of such concepts” as it appears to “…limit flexibility, process creation and entrepreneurial behaviour”.
But, supply chains are a function that requires discipline to achieve the agreed plan and that requires structured processes. For organisations with multiple supply chain operations across one or many countries, standardisation should be a non-negotiable goal. For a 3PL, differences in processes for particular clients should be written as addendums to the standard process.
Managers in supply chains
While the whitepaper provides valid opinions concerning people relations across an organisation’s supply chains, the suggested approach has existed for some time. In 2006, the Boston Consulting Group published a report that considered the role of managers in supply chains. Its conclusions were:
- be a continual learner
- have an international perspective
- operate within different cultures and global markets
- have an adaptable management style to work with three generations
- respond to the motivations of a diverse workforce
- develop incentives to attract and retain talented staff
- structure a work environment that encourages and recognises the performance of teams
The current whitepaper contains a similar summary, but adds that managers should also use collaborative IT platforms. This illustrates that between 2006 and 2019, the factors for managers working in supply chains has hardly changed. The challenge is for managers to consciously adopt this approach.